Sind ungeplante Ausfallzeiten ein großes Risiko für Ihre Produktion? Ändern Sie häufig Ihre Produktionslinien? Stellen Sie sich vor, Sie hätten eine leistungsstarke Lösung zur Hand: ein zentrales Wissensarchiv für Ihre gesamte Produktionsanlage. Ein Digitaler Zwilling, der nicht nur Ausfallzeiten reduziert oder verhindert, sondern Sie auch unabhängig von dem Wissen macht, das in den Köpfen Ihres Wartungsteams und Ihrer Lieferanten gespeichert ist. Mit stets aktuellen Daten, die von Ihrem eigenen technischen Personal vor Ort einfach gepflegt werden können, behalten Sie die Kontrolle über Ihre Produktionseffizienz wie nie zuvor.
Sowohl Pharmafabriken als auch Fabriken der Lebensmittelindustrie arbeiten mit gefährlichen Materialien und stellen extrem hohe Anforderungen an Reinräume. Die dort verwendete Technologie ist empfindlich, und Fehler können hohe Kosten verursachen – im schlimmsten Fall können sogar Menschenleben in Gefahr geraten.
OrthoGraph und Operational BIM zielen nicht nur auf die Kostenreduzierung in diesen Bereichen ab, sondern bieten auch ein Werkzeug, das sowohl die Risiken von Ausfallzeiten als auch die Sicherheit der Menschen bei Eingriffen erheblich reduziert.
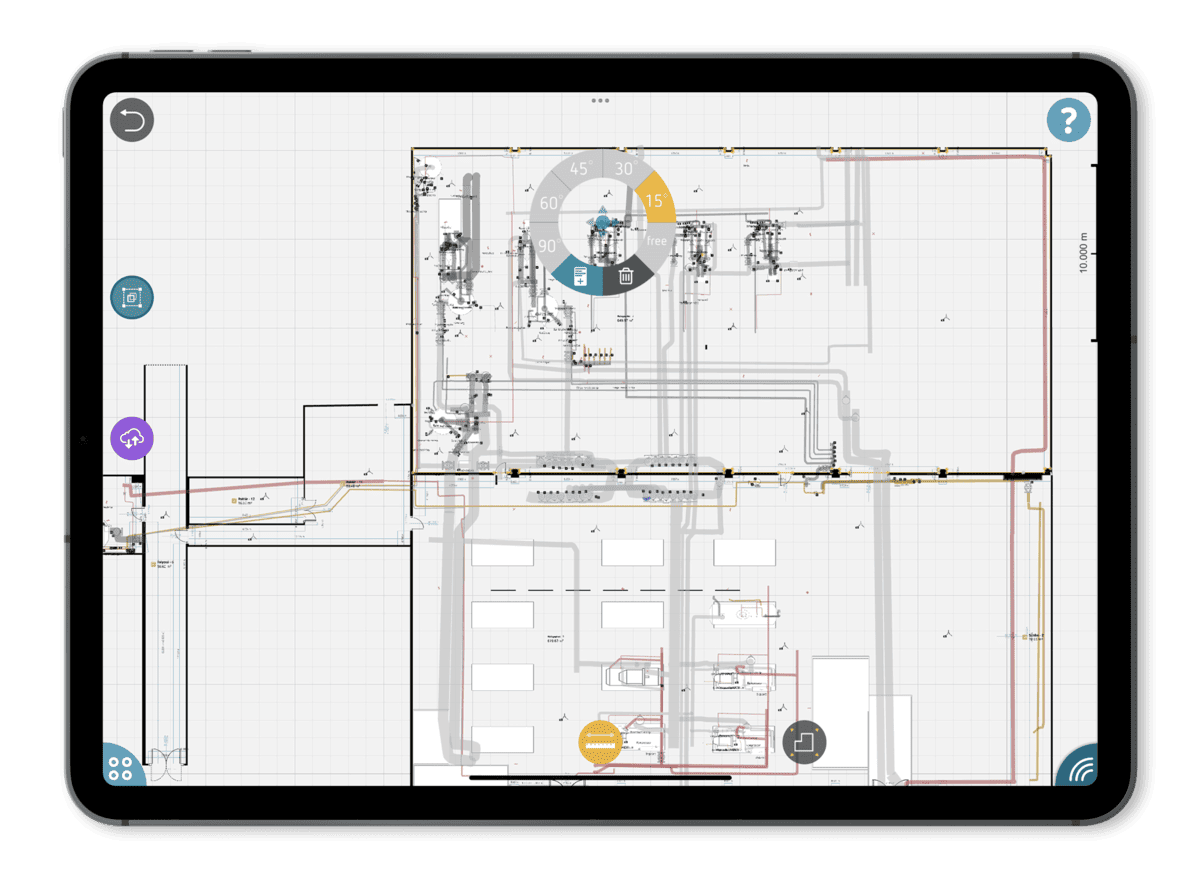
Menschenleben retten:
Stellen Sie sich vor, Sie haben ein detailliertes 3D-Modell, das alle Rohre, Ventile, Messgeräte und Einheiten enthält, die Teil der Wartungsarbeiten sind. Diese Komponenten sind mit QR-Codes oder RFID-Identifikatoren versehen, und alle wichtigen Parameter sind digital mit ihnen verknüpft. Außerdem verfügen Sie über Panoramafotos an jeder wichtigen Position. Stellen Sie sich vor, all diese Daten werden innerhalb weniger Wochen gesammelt und können von Ihrem Wartungspersonal als Teil ihrer regulären Arbeitsabläufe mühelos auf dem neuesten Stand gehalten werden.
Das bedeutet, dass die Feuerwehrkräfte den Standort über einen klar definierten Weg anhand der Panoramafotos erreichen können, das richtige Ventil finden und sicherstellen können, dass sie mit dem richtigen Ventil arbeiten, bevor sie etwas anderes schließen. So wird das Risiko zusätzlicher Unfälle minimiert. Und wir wissen alle, dass sie unter Druck arbeiten – Fehler können tödlich sein, daher ist es entscheidend, sie zu minimieren.
Dies spart Zeit und reduziert Risiken, wodurch Leben gleichzeitig geschützt werden.
Geld sparen:
In vielen Fällen wird die meiste Zeit während des Betriebs damit verbracht, die richtige Ausrüstung zu finden. Es kann sogar vorkommen, dass nicht das richtige Objekt gewartet wird, sondern ein ähnliches in der Nähe. Haben Sie das schon einmal erlebt? Das ist verständlich, denn in einem „Ventilwald“ das richtige Ventil zu finden, ist manchmal eine große Herausforderung.
In OrthoGraph haben alle Wartungspunkte eigene Referenzlinks, und wir empfehlen außerdem, eindeutige Kennzeichnungen für alle Objekte zu verwenden. Um den Wartungstechniker zum richtigen Ventil zu schicken, senden Sie einfach den entsprechenden Link, und OrthoGraph zeigt es sofort an. Sowohl der Techniker – mit einem iPad – als auch der Teamleiter – im Webbrowser im Büro – können genau sehen, wo sich der spezifische Wartungspunkt in 2D und 3D befindet.
Diese erhebliche Zeitersparnis bedeutet, dass dasselbe Personal mehr erledigen kann. Außerdem kann dank der elektronischen Dokumentation derselben Daten die gleiche Servicequalität erwartet werden – unabhängig davon, welcher Techniker die Wartung durchführt.
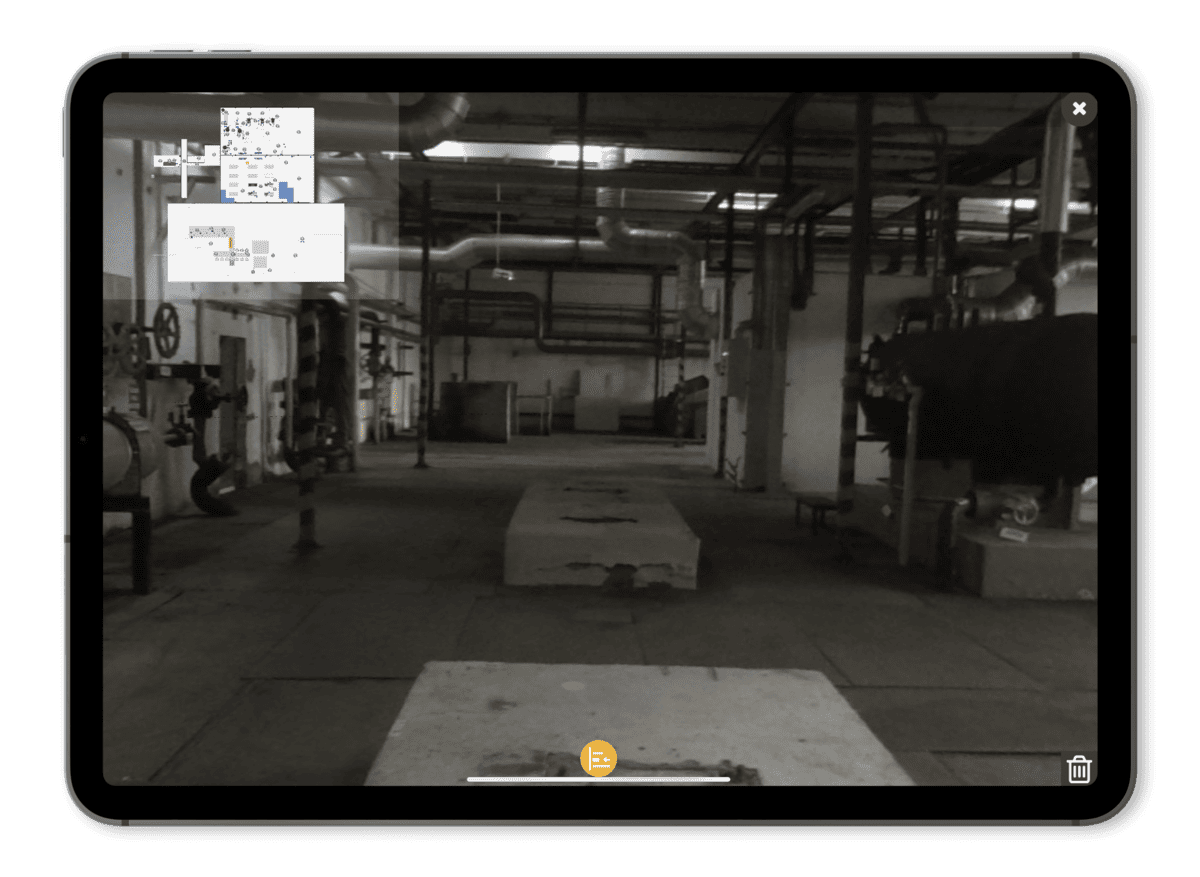
Wissen, dass das richtige Gerät repariert wurde:
Wir betonen stets die Bedeutung von eindeutigen Kennzeichnungen an jedem Wartungspunkt. Nicht nur an jeder Maschine, sondern möglicherweise sogar an verschiedenen Teilen davon, wenn es so entscheidend ist, die Vorgänge zu kontrollieren. Indem der Techniker aufgefordert wird, die entsprechende RFID-, QR-Code- oder Barcode-Kennzeichnung zu scannen, wird sichergestellt, dass das richtige Objekt gewartet wird. Noch besser: Wenn ein SLA-Vertrag mit einem Subunternehmer besteht, können wir sogar registrieren, wann das jeweilige Objekt betreten oder bearbeitet wurde.
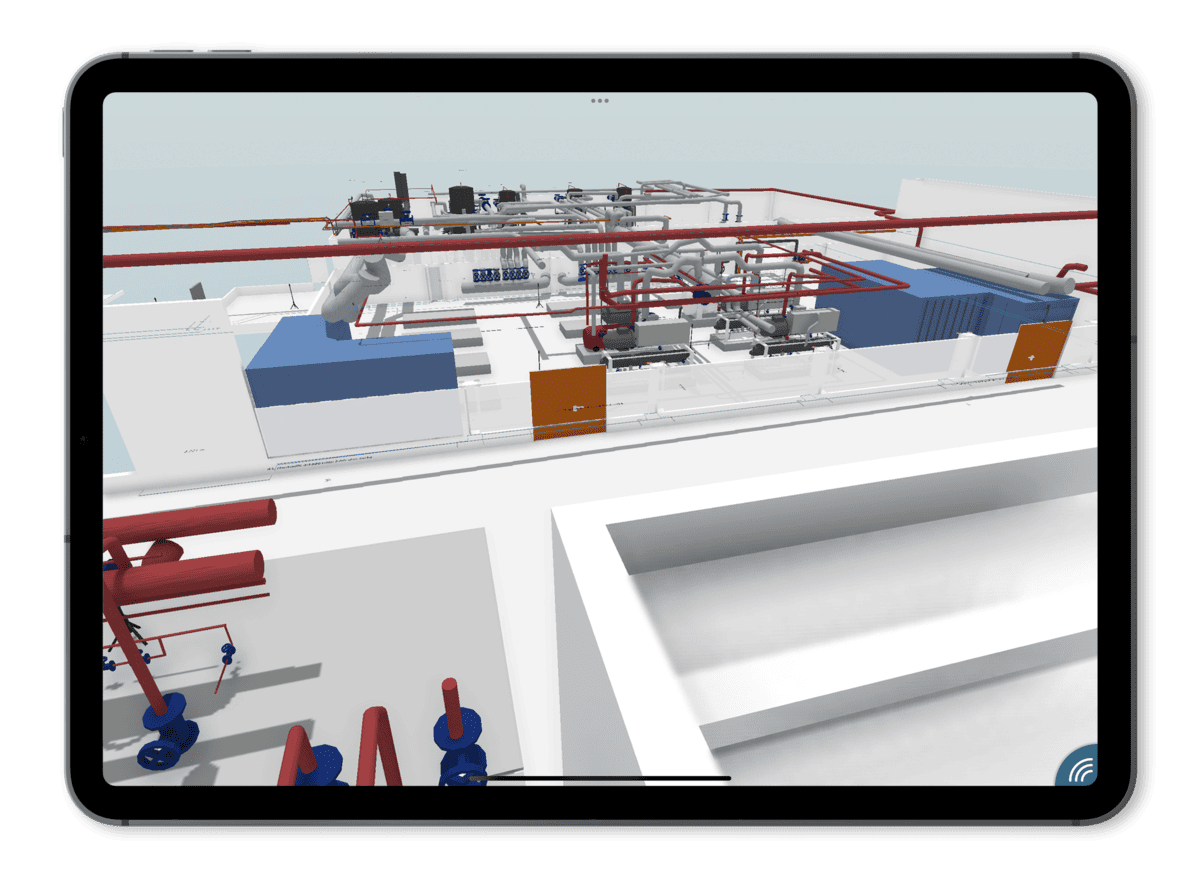
Daten aktuell halten:
Das Erfassen von Gebäude- und Anlagendokumentationen ist zeitaufwendig, aber deren Aktualisierung ist noch schwieriger. Zumindest war das bisher so. Mit OrthoGraph wird es so einfach, dass innerhalb weniger Stunden gelernt werden kann, wie alle Inventaränderungen, Objektbewegungen und Austauschvorgänge in der Fabrik dokumentiert werden. Das bedeutet, dass jeder Techniker, der eine Reparatur durchführt, Änderungen einfach dokumentieren, neue Fotos machen und sie dem entsprechenden Gerät zuordnen kann. So entsteht eine stets aktuelle Gebäude- und Anlagendokumentation. Dies schafft Unabhängigkeit: Sobald eine neue Aufgabe an einem bestimmten Objekt erledigt werden muss, ist es leicht zu finden, und alle zugehörigen Eigenschaften und Dokumentationen können mit OrthoGraph aufgerufen werden – entweder vor Ort oder direkt am Arbeitsplatz.
Wenn eine Produktionskette geändert, umgebaut oder verlegt wird, können all diese Änderungen sofort in OrthoGraph erfasst werden, sodass alle verbundenen Systeme – CMMS, Automatisierung, Überwachung usw. – über die Änderungen informiert werden. Später, wenn beispielsweise eine Übertemperatur oder ein Überdruck auftritt, weiß jeder, wo dies geschieht, und kann so schnell wie möglich handeln.
Auch Änderungen an Grundrissen können manchmal vorkommen: Wände, Türen und Fenster werden modifiziert. Diese Änderungen können ebenfalls von eigenen Mitarbeitern erfasst werden, obwohl wir empfehlen, für diese Aufgabe diejenigen Techniker auszuwählen, die ein besonderes Talent für Technologie haben. Während Inventaränderungen so einfach sind wie das Schreiben eines Beitrags auf einer Social-Media-Plattform, erfordert das Ändern der Hauptgrundrisselemente etwas mehr. Nicht viel, aber es benötigt eine dreitägige Schulung, um zu lernen, wie man dies professionell und digital gesteuert durchführt. Es sind keine architektonischen Kenntnisse oder eine spezielle Ausbildung erforderlich, aber ein gutes räumliches Verständnis und die Fähigkeit, Grundrisse zu lesen, sind notwendig. Das Verfolgen dieser Änderungen mit dem richtigen Wissen dauert erneut nur Stunden, vielleicht einen Tag, aber nicht mehr.
Integration – das Beste aus Operational BIM herausholen:
Daten schaffen nur dann Wert, wenn sie genutzt und gepflegt werden. OrthoGraph ist eine Plattform als Datenhub. Jedes System, das Gebäude- oder Anlagendaten, grafische Darstellungen oder Berichte benötigt, kann sich mit OrthoGraph integrieren. Die API ist dafür kostenlos nutzbar und integrierbar. Je mehr Systeme mit OrthoGraph verbunden sind, desto mehr Wert kann daraus generiert werden.
Eine ordnungsgemäße Integration in ein CMMS-System ermöglicht schnelle und kontrollierte Arbeitsabläufe – auch durch die Nutzung eindeutiger Identifikatoren für alle Objekte. Ein Gebäude- oder Maschinenautomatisierungssystem kann problemlos überwachen, was in der Fabrik geschieht, und schnell reagieren, wenn etwas außerhalb des normalen Bereichs liegt. Selbst ein Finanzsystem kann grafische Berichte über die am schlechtesten oder besten funktionierenden Maschinen erstellen, die mit anderen verglichen werden sollten, um die Leistung auf das höchste Niveau zu bringen.
Berichte zu erstellen bedeutet, das Maximum aus dem integrierten Operational BIM-Ökosystem herauszuholen, indem Daten kontinuierlich analysiert werden. Künstliche Intelligenz könnte viel leisten, aber eine Person mit einer guten finanziellen Perspektive kann dies bereits heute tun. Wir nennen diese Rolle bewusst nicht BIM-Manager, da dies keine Person mit architektonischen oder ingenieurtechnischen Kenntnissen sein muss. Vielmehr kann eine prozessorientiert denkende Person mit finanziellem Hintergrund die entscheidenden Schwachstellen identifizieren, die sich kritisch auf die aktuelle Leistung auswirken. Mit diesem Ansatz kann OrthoGraph Operational BIM, gesteuert durch diese Person, durch die Verbesserung der Leistung sofort Geld generieren, indem Schwachstellen hervorgehoben und adressiert werden.
Was gewinnen wir noch, wenn wir eindeutige Kennzeichnungen, RFIDs, QR-Codes oder Barcodes an allen Wartungspunkten verwenden?
Exakte Elementidentifikation und Workflow-Kontrolle. Wenn wir ein wichtiges Objekt oder Gerät haben, das aus irgendeinem Grund bearbeitet werden muss, können diese eindeutigen Kennzeichnungen dabei helfen, das jeweilige Objekt leicht zu identifizieren. Wenn wir ein workflowbasiertes Issue-Tracking-System verwenden, das auf diesen Kennzeichnungen basiert, kann der vor Ort tätige Mitarbeiter aufgefordert werden, die Kennzeichnung des betreffenden Geräts zu scannen, um zu bestätigen, dass das richtige gewartet wird. Ist das System darauf vorbereitet, können wir sogar die Arbeitszeit überprüfen, um weitere Informationen über die durchgeführte Arbeit zu erhalten.
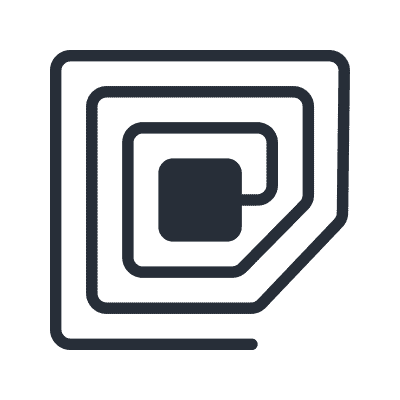
Haben Sie ein ähnliches Projekt im Sinn? Haben Sie weitere Fragen? Möchten Sie mehr in einem persönlichen Meeting erfahren oder ein Pilotprojekt starten? Klicken Sie auf den Button:
zu unserem Newsletter
OrthoGraph

Kontaktieren Sie uns
Kontaktieren Sie uns
OrthoGraph GmbH
Gartenstrasse 7
Zug
Schweiz
6300
+ 41 (41) 5510150
9:00-18:00 Zürcher Zeit
USA: +1 760 933 1550
UK: +44 (20) 34119438
Andere Seiten
Bildung
Schnelles Aufmaßkonzept
OrthoGraph für Bauprojekte
Aufmaß historischer Gebäude
Recent Comments