Cost reduction, energy optimization, fulfilling ESG needs are key goals of these segments too. Sometimes even more, the safety of people, anti-terrorism intervention planning etc. is also a special role in these buildings. Sometimes data safety is also a key issue, but not only about how and where the data is stored, but also about how it is captured. By using OrthoGraph, uniquely, anyone who got the 3 days long technical training, and has the simplest surveying tools such as a laser distance meter and an iPad can do the job.
Let’s see what benefits can be produced out of an OrthoGraph Operational BIM in short and long term in Governmental, Municipal and Public buildings.
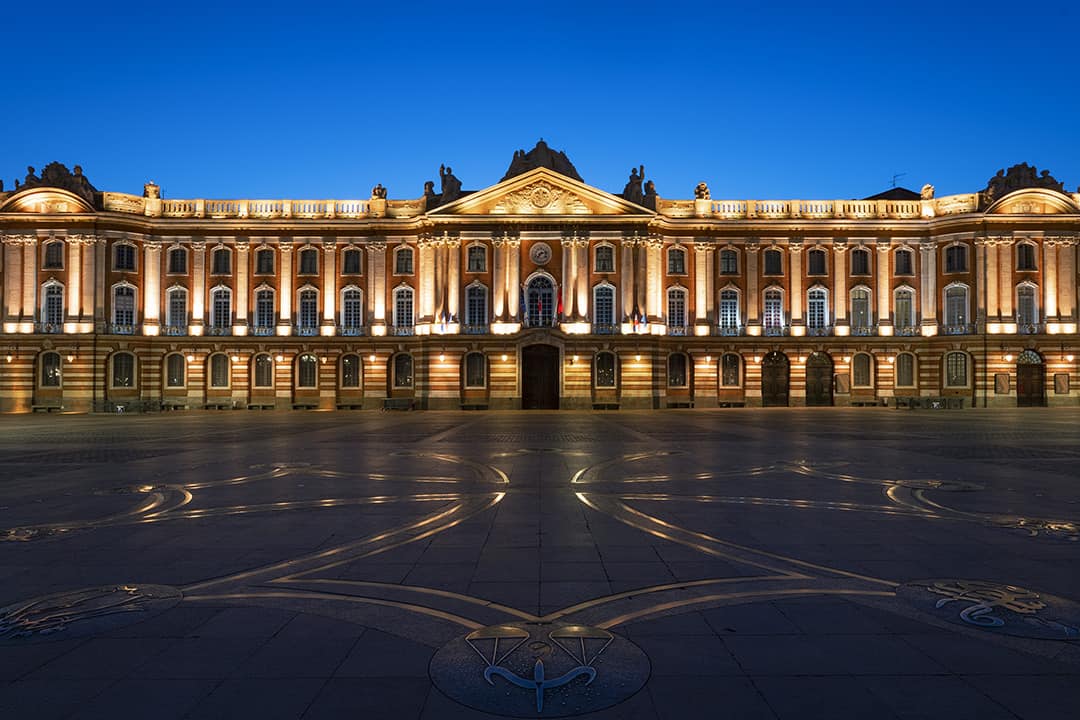
Instant energy cost reduction:
The most expensive energy is the wasted energy. In case of a large building collecting all external openings and recording their condition, main properties, dimensions, probably thermal images and photos one by one is an impossible mission. But now with OrthoGraph. It’s not necessary to setup an overall high-cost renovation of all openings which might not be even feasible, on the other hand it’s hard to allocate the budget for that. By using OrthoGraph any technician can record the necessary data, assign thermal images using low-cost tools to any opening, wall segment or large consumer thus making it possible to set individual plans for each of them. By assigning and using unique identifiers on them such as RFID tags, QRCodes or barcodes you can be sure that both tendering and then the renovation work can be the best performing, minimal cost providing the best results, thus the shortest ROI. At the same time, reuse the same data for other purposes too. To tender and contract cleaning or to make reports about building performance.
Operational BIM can save human lives:
There might be situations where clean, and accurate building knowledge, panorama camera shorts might be essential for safety interventions. It can be an unexpected fire, earth-quake, or a terrorist action where the preventive planning saves lives both on people in the building, and people coming to rescue them.
By using OrthoGraph temporary access can be given to the people, organization who actively processes the intervention. By using a simple web browser in a notebook or a tablet all allowed people can access and see the full building in 2D or 3D, including all attached photos and panoramas too. Sometimes it’s easier to break through a partition wall than to bring people out through a risky area, maybe fighting with the fire. The accuracy of OrthoGraph’s Operational BIM is that good, then intervention plans can easily made based on the data for any kind of safety action.
How is the data created?
Basically we always recommend ordering the surveying services from Certified OrthoGraph Surveyors. OrthoGraph can easily be learned, and the use of the system doesn’t need high expertise, architectural or similar high-educational knowledge. Anyone having a 3D space understanding can do the floor-plan surveying / modelling, and the graphical asset inventory can be done with even less knowledge / expertise. The most important is always the specification / planning of data capturing – by clearly defining the goals – and the local quality control. Even though OrthoGraph does a strong quality control on surveying and inventory data capture, the existence of some building elements – e.g. columns, pillars, machines etc. – should be checked by someone doing the on-site quality assurance.
All results are produced on-site, and can be accessed from anywhere having the proper access rights.
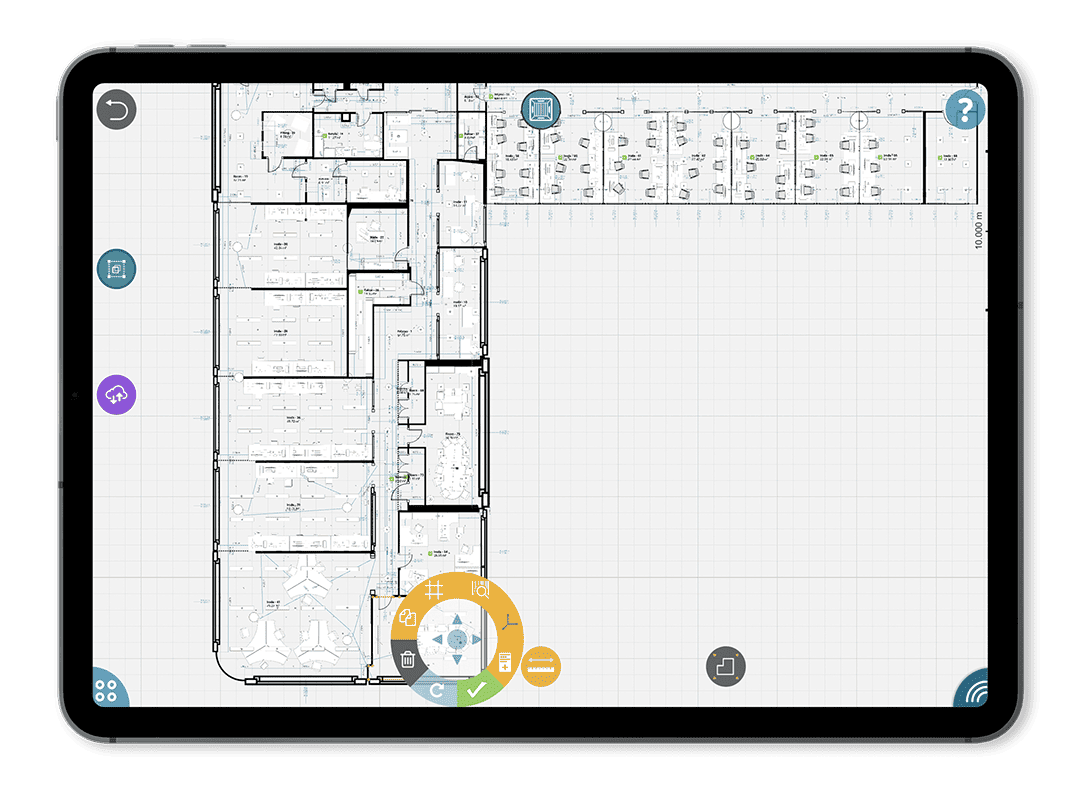
How will be the data kept fresh?
When there is the data captured, then the best way to keep it updated is to start using it. The more benefits you get out from it, the better quality data you will continuously get. The regular technicians can keep the 3D model and inventory updated as part of their onsite jobs, without any special knowledge, after a short training. When there are floor plan changes, then a bit higher experienced surveyor is required, which knowledge can be gathered in our 3 days long OrthoGraph Certified Surveyor technical training. So if there is a technician with better 3D visual understanding, then you have already the in-house resource for the successful documentation of any layout / floor plan changes. OrthoGraph stores everything versioned, so if there is a demand to look back how the building looked like a month ago, then just ask OrthoGraph and you will see the exact documentation for the given timepoint.
Where is the data stored?
We know data is sensitive. In these segments even more than regularly, as there are locations and people in them with higher risk or higher level of safety required. To store and access data only with proper user rights OrthoGraph has an well established, enterprise level user access right management system.
In some cases our clients have a demand to keep all data, documentation in-house physically, so nothing should leave the premises of them. To support this OrthoGraph Cloud can be installed on-premise, and the mobile part of the system can easily be configured only to communicate with the given on-premise server. This means that even we, as the technology manufacturer cannot access anything running at the client. We only get summarized information of the total system use for licensing purposes, that can also be controlled by the IT department of the client. On-premise installation also contains a training of local IT professionals and the creating of a dedicated on-premise system maintenance documentation. This way the local system can be operated and maintained by the local professionals of the end-user.
What else do we get, if we use unique identifiers, RFIDs / QRCodes or barcodes on all maintenance points?
Exact element identification and workflow control. If we have an important object, equipment that needs to be touched for any reason, then these unique identifiers can help to easily identify the given object. If we use the proper workflow based issue tracking system that is based on using these unique identifiers, then the site worker can be requested to scan the given equipment’s identifier to confirm that the proper one is going to be maintained. If the system is prepared for that, then we even can check the time of work to find our more information about the given work.
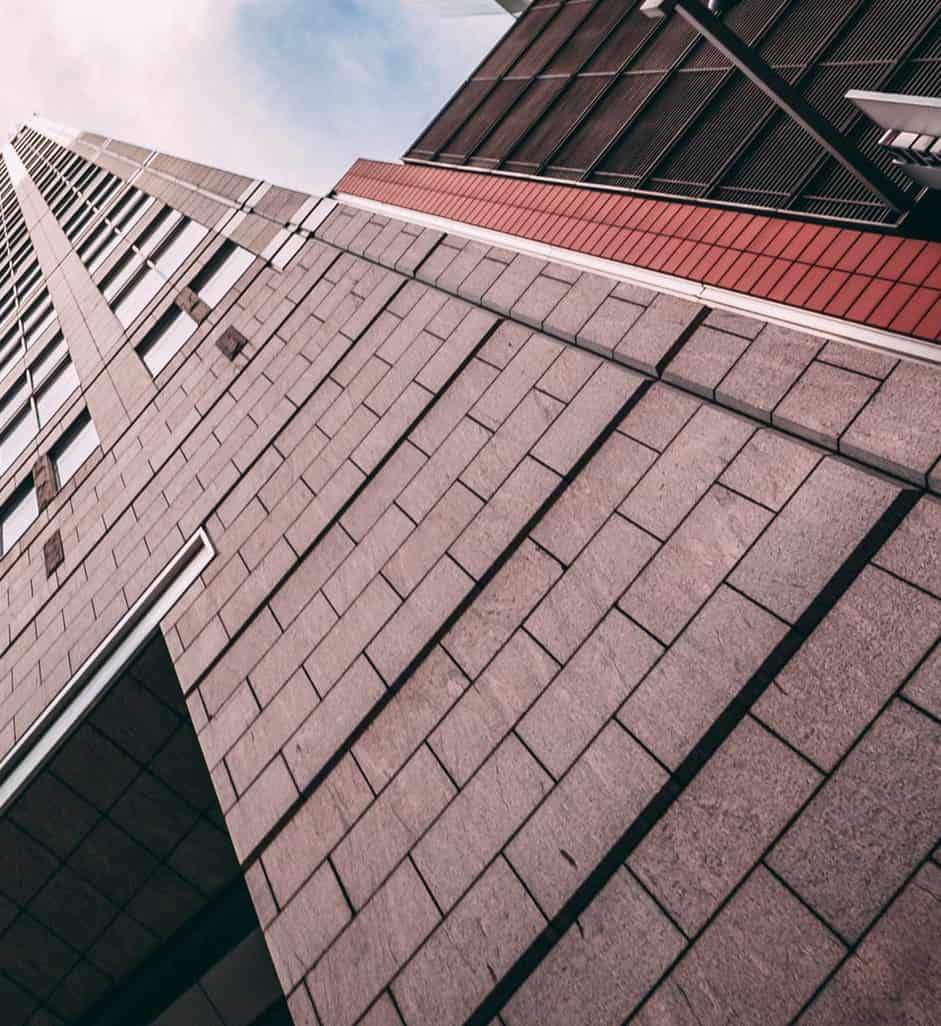
Capture only real value, that you are going to use, and use the right tools for the right purpose!
Many times we get the request to capture everything in the BIM as it should represent all content of the building. In reality most of piping, cable channels, detailed statue represntations don’t have any value in the BIM. All these can easily be captured using laser scanned point clouds, which is not going to be only cheaper, but it will be more usable in the future to support refurbishment, building changes. These are typically data that is rarely required, but when they are required, then with the highest possible accuracy. This is another reason to combine technologies and to choose the proper ones for the required functionality.
Simply BIM needs maintenance points and all other graphical materials should be recorded in point clouds, made at the right moment of construction – right before having them covered.
Have you got a similar project in your mind? Have you got further questions? Want know more in a personal meeting or want to start a pilot? Click the button:
to our Newsletter
OrthoGraph

Contact us
Contact us
OrthoGraph GmbH
Gartenstrasse 7
Zug
Switzerland
6300
+ 41 (41) 5510150
9:00-18:00 Zurich Time
USA: +17609331550
UK : + 44 (20) 34119438
Other pages
Education
Rapid Survey Concept
Orthograph for Constructions
Historical Building Survey
Recent Comments