Maintenance Management
Expected cost: Performance of a graphic inventory on one occasion, monitoring of larger moves and remodeling work
Products used: rthoGraph Enterprise, CMMS, Leica BLK360
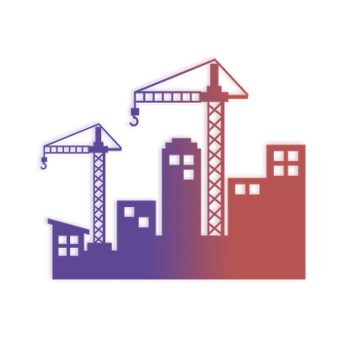
This functional part most probably results in the greatest savings, which, in addition to ensuring a reduction of costs, also involves an improvement in the quality of the property operation service. This is partly a result of the lower maintenance personnel demand, the comprehensible maintenance processes, prompt communication, the significantly shortened travelling and element-locating time, and the up-to-date building documentation created as a “side product”.
With the implementation of suitably scheduled and planned maintenance work the number of unexpected breakdowns and outages can be reduced, which can be further improved by connecting the building automation and production line analysis systems to the operation of the CMMS system. Through this, in addition to the fewer downtimes, the maintenance cycles can be extended to correspond to the actual use, meaning that the filter in a fan coil unit only has to be replaced if was made necessary due to the amount of use.
It is important to note that the planned downtimes can result in even more savings in many cases, such as lower back-office service costs. Unexpected downtimes occurring on the manufacturing, production side of enterprises can cause outages of main activity, due to this well-planned and implemented facility management indirectly results in even greater savings than merely a reduction of the daily operation overheads.
The greatest advantages of the OrthoGraph-CAFM/CMMS system pair can be found in the following areas of maintenance work:
Building documentation that can be used for measurements at any time
Expected cost: 0% if scanned building documentation is already available in the course of any construction or remodeling work
Products used: Leica BLK360
It is best if there is the opportunity to survey all building engineering elements, cabling, ducting and all other data to be concealed in the course of the construction or refurbishment of buildings. This has to be performed with the Leica BLK360 laser scanner which records the current, precise and measurable status image of the site.
The documentation created in this way can be used effectively for the planning of later reconstruction or extension work and for minimizing the costs involved. If the requirement, for example, is to create the water supply connection for a new shower unit, by using the measurable panorama views recorded by the Leica BLK360 during the construction or reconstruction, the water pipes and connections available in the wall can be located at precision under 1 cm. It is then sufficient to dismantle just that few square centimeters where the water connection needs to be installed. This reduces construction costs and a great deal of working time, because the locations can be handed back more quickly and put to work.
In case of an unexpected fault, damage or emergency it is advantageous to find out precisely how the given room, building section or engineering block looked. Faults may occur in gas, water or electric lines when their environment has to be checked for the presence of other systems that could represent a significant risk of damage before repair work is started. In situations like these the Leica BLK360 system may be used in order to minimize damage and injury, or, in the worst case, to provide evidence of the given situation before the event. In all cases by using the Leica BLK360 application the data can be retrieved immediately and inspected even on-site.
Effective finding and repairing of burst pipes and thermal bridges
Expected cost: the price of one or two laser scans
Products used: Leica BLK360
The Leica BLK360 system also has its own thermal camera. This means that in addition to panorama images and point clouds, fully corresponding horizontal thermal camera panorama images are also available.
It is in the most rare of cases that the damp patch occurs precisely at the location of a burst pipe. Using a thermal camera image and then the point cloud the coldest or warmest point, i.e. the source of the fault, can be located with high precision.
This same solution can also show the locations of thermal bridges and bad insulation, in other words it can be easily seen where the building’s heat loss can be reduced, which in turn will result in saving of energy and improvement in comfort too.
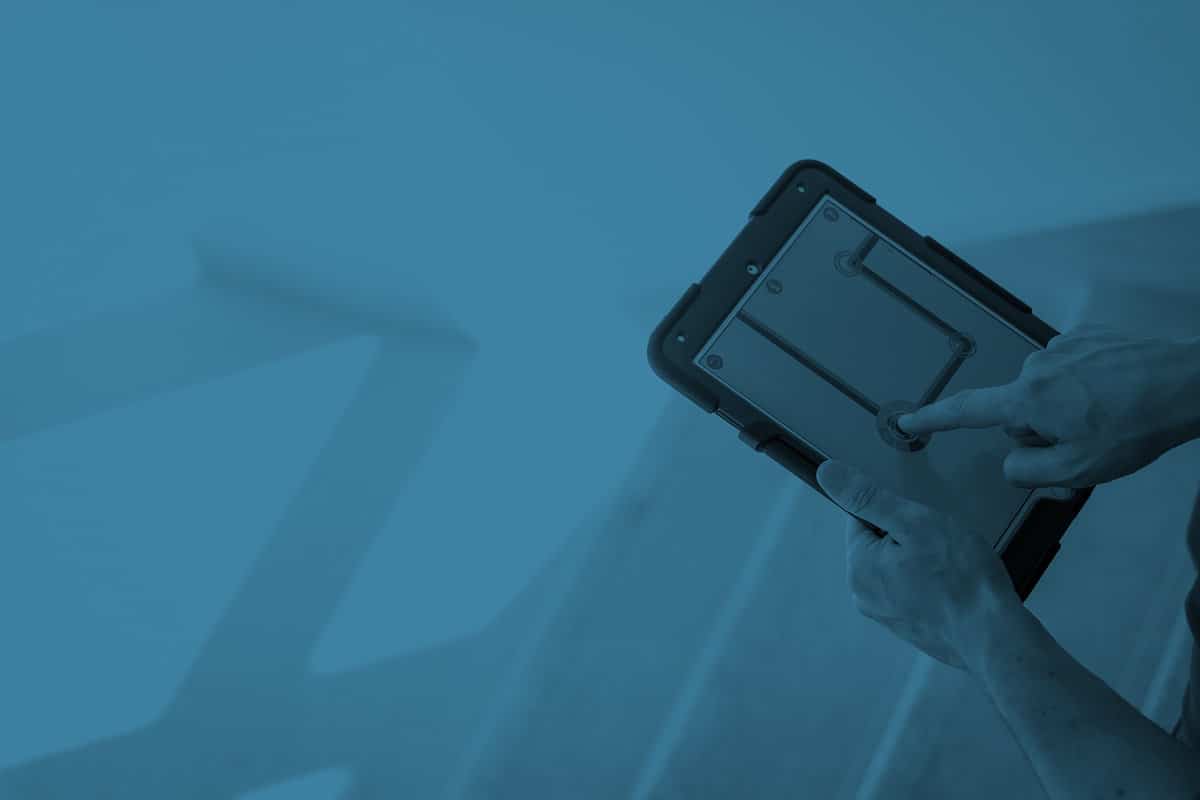
Building and asset documentation available anywhere at any time
Expected cost: 0% if scanned building documentation made during the construction or reconstruction work is available
Products used: OrthoGraph, Leica BLK360, ArchiFM
When maintenance work is being carried out it is at the place where the work is being done that there is the most need for knowledge of the features of the equipment to be maintained along with its documentation. Savings can be made if you know if a given device is under guarantee or not, or if you can watch a video on how to take it apart and repair it, or if you can read through the detailed maintenance description whenever you want. In many cases even finding the device that needs maintenance represents a problem.
Finding and identifying devices quickly
When issuing maintenance work, the simplest way of providing the instructions is using web links to the devices appearing in the BIM models. In this way the given element can be displayed immediately in the floor plan in 2D or 3D view using a simple web browser, and if you touch the given link on a mobile device, OrthoGraph opens the BIM model and all related documentation forthwith.
The OrthoGraph system helps you find the equipment that needs repairing with barcode or NFC chip technology. The user is able to generally or precisely localise the given device with the 2D or 3D graphic floor plan, then by reading the barcode the OrthoGraph system will confirm whether they have found the right device or not.
Maintenance history and documentation at hand
After you have found the right device, OrthoGraph gives you full BIM model access, so you can even view the attached photographs (if any were taken, such as of a fan-coil before a suspended ceiling is installed), check out the corresponding features, but what is perhaps the most important: the ArchiFM system can be called up instantaneously for the given element.
The ArchiFM system maintenance module allows you immediate access to guarantee information, installation information, any attached documentation or even the maintenance history for the given device. Using the history it is easy to discover if a frequent fault is being caused, say, by bad dimensioning, and if it would be more economic to replace the element rather than repairing it again and again.
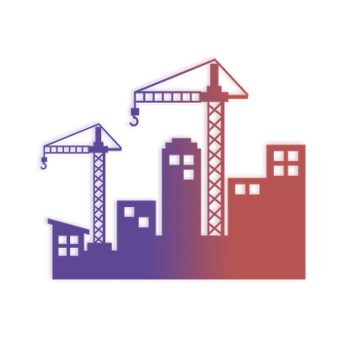
Planned downtime instead of a fault, with minimal repair times
As a result of the attached videos or sound recordings the maintenance personnel gain fast access to repair information, which is easier to interpret than just following the maintenance instructions to the end. They can precisely see the fitting or greasing points and how to approach them safely. In addition, if a video or sound recording is made when a system is installed or when operating correctly and is attached to the given device, then later on, in the course of a simple inspection they can detect that a fault is approaching on the basis of the sound alone, in other words it can be repaired in the scope of planned maintenance instead of an unexpected shutdown. Planned maintenance and downtimes do not only mean a reduction in repair costs of the device, but the productive activities can also be protected from unexpected outages, resulting in even greater savings.
Optimised instructions, effective communication
Shorter travelling times and more effective communication between the maintenance personnel and the staff issuing the work also result in significant savings. The exact tasks can be sent easily to the mobile devices carried by the maintenance staff, and, the other way around, the devices to be maintained on-site can be easily referenced for approval. With this the need to travel between the site and headquarters disappears completely, as the documentation is available on-site immediately.
This does not only make it possible to employ fewer maintenance personnel, but as a consequence of the availability of electronic documentation, staff changes would not affect the quality or efficiency of the operation of the property.
This more effective level of communication can mean a lower demand for personnel and also an increase in the quality of the service.
Job shopping
An incidental result of the solution is that, if required, the job shopping process can also be introduced, in other words maintenance personnel who become freed up can apply to do the task closest to them or that is the most interesting, which means that they are solved not only faster but in more efficiently allocated way, and all this can be completely automated.
Leica BLK360 point cloud in planning and work accounting
The documentation available in the Leica BLK360 system can result in significant savings in finding the engineering element involved, quickly determining dimensions and surfaces, and identifying burst pipes and thermal bridges even on-site, the advantages of which are detailed in the previous points.
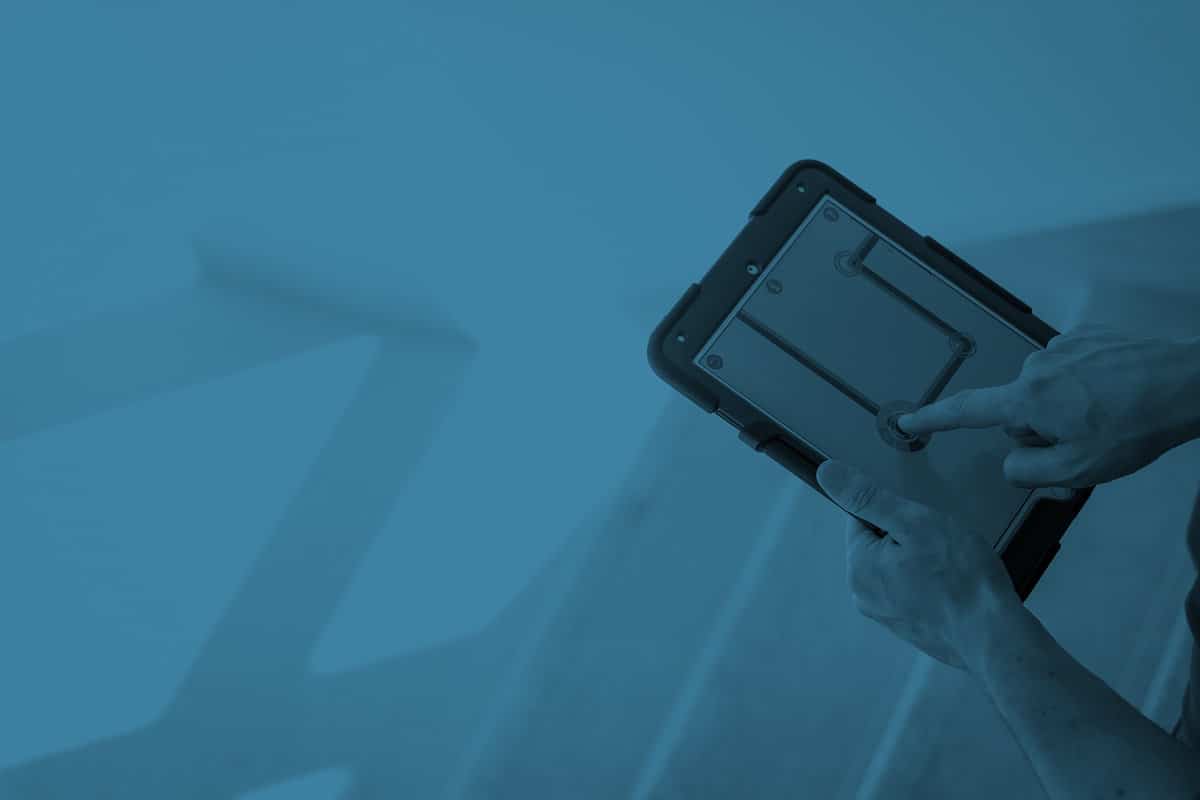
Graphic fault reporting interface
Expected cost: 0% if an up-to-date building model is available in connection with the operation of the property
Products used: OrthoGraph, CMMS/Ticketing system
The main advantages of the OrthoGraph BIM models are multiple utilizations and the simplicity of keeping them updated. If the Orthograph model of a building is available and it is used in daily operation and maintenance whenever possible, a graphic fault reporting interface is provided as a side product of this for the tenants and employees using the property. This means that anyone who sees or hears a fault can use a simple web browser to call up the 2D or 3D model of the building, and then by clicking on any element in it they can automatically call up the breakdown reporting interface. A fault ticket is automatically generated after the seen or heard problem has been entered and that ticket then starts its life immediately through the maintenance system.
The fault tickets are handled by the maintenance management system, which means the handling of the entire process with priority levels and even with the use of approval levels. The persons reporting the faults can check their current status, and even receive information on this via automatic e-mail notification. In addition, if system implementation has been suitably carried out, even completely automated job shopping can be achieved, i.e. the expected reaction times to fault reports can be reduced significantly. This does not only result in lower costs, but also in greater customer satisfaction without increasing the number of maintenance personnel.
Since the fault tickets get into the helpdesk system via the 2D/3D building model, the number of fault dispatcher personnel can be reduced, or the position may even be terminated altogether.
The same interface can be built into any other building-related service, such as the meeting room reservation system, the cleaning demand system or even for access to the building automation system.
It is important to note that these administered buildings are not displayed in the system in static condition that has to be periodically updated after remodeling work and function changes, instead the one and common actual BIM model is always automatically displayed, in plain English the system has no administration costs whatsoever.
Planned maintenance instead of faults
Expected cost: 0.1% if an up-to-date building model is available in connection with the operation of the property
Products used: OrthoGraph, CMMSe
The ArchiFM Maintenance system has a professional breakdown maintenance module. This means that the handling of fault tickets is entirely process management based, and takes place so that it is integrated into the planned maintenance workflow.
Through planned maintenance the operation of buildings and equipment can be planned and monitored, so by performing inspections, faults and unexpected outages can be avoided.
As all maintenance activities and processes appear at a uniform place, in many cases these can be combined and efficiently scheduled, i.e. tasks related to a fault and then to planned maintenance following one another can be avoided, instead, all necessary work can be carried out at the same time.
In the course of the issue of maintenance work the approval steps and roles, persons responsible and the designation of the maintenance personnel performing the work can be adjusted to correspond with the company’s operation regulations.
Work can be issued to the maintenance staff using printed worksheets, but this can also be carried out entirely digitally using mobile devices.
Since all maintenance work is recorded via a process and system, the settling of accounts with subcontractors takes place in a uniform, precise manner. This is reinforced by the system of the Leica BLK360 which makes it possible to settle accounts on the basis of real data.
Condition-dependent maintenance work
Expected cost: 0% if the maintenance tasks performed on the basis of measured data have been connected to the ArchiFM system
Products used: ArchiFM
If the buildings and equipment have an automated management system, their performance, consumption can be measured, and if there is a more serious resonance analysis system installed, then the data arriving from these can be used as the basis of maintenance work. This means that in AC units it may be sufficient to schedule filter replacement on the basis of actual use, which will reduce both labour and material costs.
A similar or even greater saving can be achieved by monitoring the condition of the production machinery or of auxiliary equipment. With a suitable analysis system the obsolescence of these and their predicted faults can be measured and thereby planned, in other words their maintenance can be scheduled before they become faulty. This results in the minimum of unplanned downtime. This leads to cost saving due to better scheduling and due to the expected smaller volume of maintenance work.
Regular maintenance and opening of equipment increase operation lifetime but generally involve risk factors. These fault probabilities are usually characterised with the bathtub curve, which means that the probability of new inputted faults rises when equipment is opened. With condition-dependent maintenance, the number of these “openings” can be minimized, and so the number of inputted faults can also be minimised.
The possibility of concluding comprehensive contracts
Expected cost: 0% if scanned building documentation was made in the course of construction or remodeling work, otherwise 0.1% of the investment cost
Products used: OrthoGraph, ArchiFM
As the OrthoGraph survey data provides a precise picture of the property portfolio, these data can be handled in a unified way in the ArchiFM system, used for drawing up reports, and so it becomes possible to conclude comprehensive operation contracts. This means that mainly in the case of a portfolio containing large buildings or a large number of buildings, instead of having many hundreds of subcontractor contracts, comprehensive, more economical subcontractor contracts can be concluded. The scheduling and monitoring of these can be performed easily in the ArchiFM system, and so at the moment the contract is concluded the amounts of work and the expectations (e.g. SLA) contained in these operation contracts are clear.
Subsequently the actual work performed, its quality and performance according to the contract can be followed by the ArchiFM system and so settling accounts with subcontractors can be carried out within a detailed framework.
Accurate building documentation is the basis of the building operation, the maintenance specialists themselves can carry out most of the updating required (e.g. equipment replacement, moves and minor remodeling work monitoring), or in the case of more extensive remodeling work this can be carried out by an external surveying company. Whoever keeps the BIM models updated, it can be performed in a much simpler way than any other solution available today.
An up-to-date BIM model is a tool that creates value constantly. Not just because of its controlled operation, but due to the many ways of reutilizing the data, which are detailed above. This value is at the same time a long-term guarantee for the efficient operation of the building, therefore its ownership has to be taken care of. With its help knowledge of the operated property portfolio is not required from the maintenance personnel, so the owner of the BIM model is able to operate the property portfolio in the most effective manner.
Guarantee work instead of paid work
Expected cost: 0% if up-to-date data are available in the OrthoGraph-ArchiFM system
Products used: OrthoGraph, ArchiFM
As every building change, and all equipment maintenance and replacements are recorded in the OrthoGraph-ArchiFM-Leica BLK360 systems, if faults occur the ArchiFM system is able to automatically schedule their repair depending on whether the given device requires guarantee or post-guarantee repair. This also means that in the case of any repair work or device replacement, the device’s new guarantee period, if it changes, must be recorded through the OrthoGraph system on-site.
Precise, up-to-date documentation can result in significant savings if it is possible to access guarantee information immediately. This information is not only available in the office, but even on-site for the maintenance personnel too.
A detailed documentation about achievable saving using OrthoGraph and ArchiFM technologies also mentioning the tools and way of their support:
Download here
to our Newsletter
OrthoGraph

Contact us
Contact us
OrthoGraph GmbH
Gartenstrasse 7
Zug
Switzerland
6300
+ 41 (41) 5510150
9:00-18:00 Zurich Time
USA: +1 760 933 1550
UK : + 44 (20) 34119438
Other pages
Education
Rapid Survey Concept
Orthograph for Constructions
Historical Building Survey