Operational BIM© ROI Calculator
– use your data to see your achievable savings –
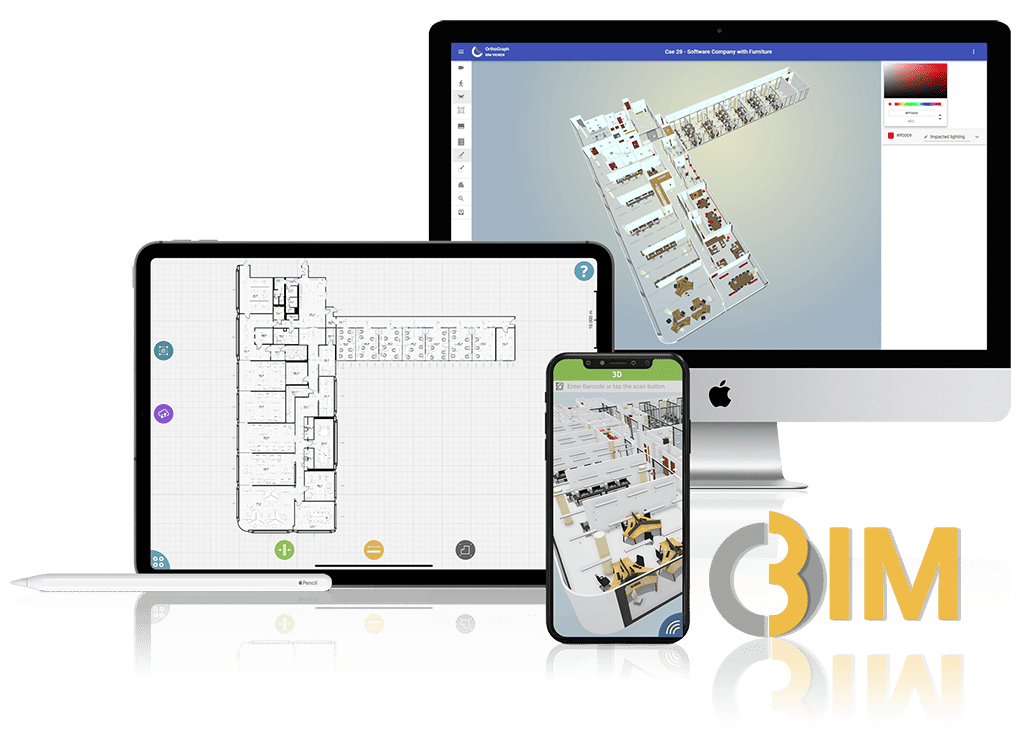
Some examples for impressive savings using Operational BIM
During building operations most property owners rely on outdated, inaccurate data of their property. Even if a new building has just been completed, in most cases only a – usually not very accurate – as-built documentation is available if any, updated from the original CAD plans. Moreover, this all becomes obsolete in weeks with instant changes after arrival of new tenants, users or simply by daily use. OrthoGraph technology gives an instant accurate 3D BIM model and graphical toolset for any new or existing old building, and all up to date.
Measuring the performance of the building
The usage effectiveness of properties are actually delimited only by the area, plot or exterior walls that contain them. Their productivity in the 30-50 year long lifecycle is a critical issue, wheter it is measured in rental fee, the capacity of patients treated in a hospital, the people seated in a university / office building or the highest productivity in a manufacturing facility. Using OrthoGraph building models, you can immediately see the breakdown of buildings by room category (useful vs. service area) even with itemized details by workplace. Using floor plans, you can immediately redesign the building to maximize your productivity. This efficiency-enhancing – in many cases also revenue-enhancing – development not only yields a very fast payback, but also tremendous results when projected onto the building’s life cycle, e.g. multiplied by the rent.
Room category division
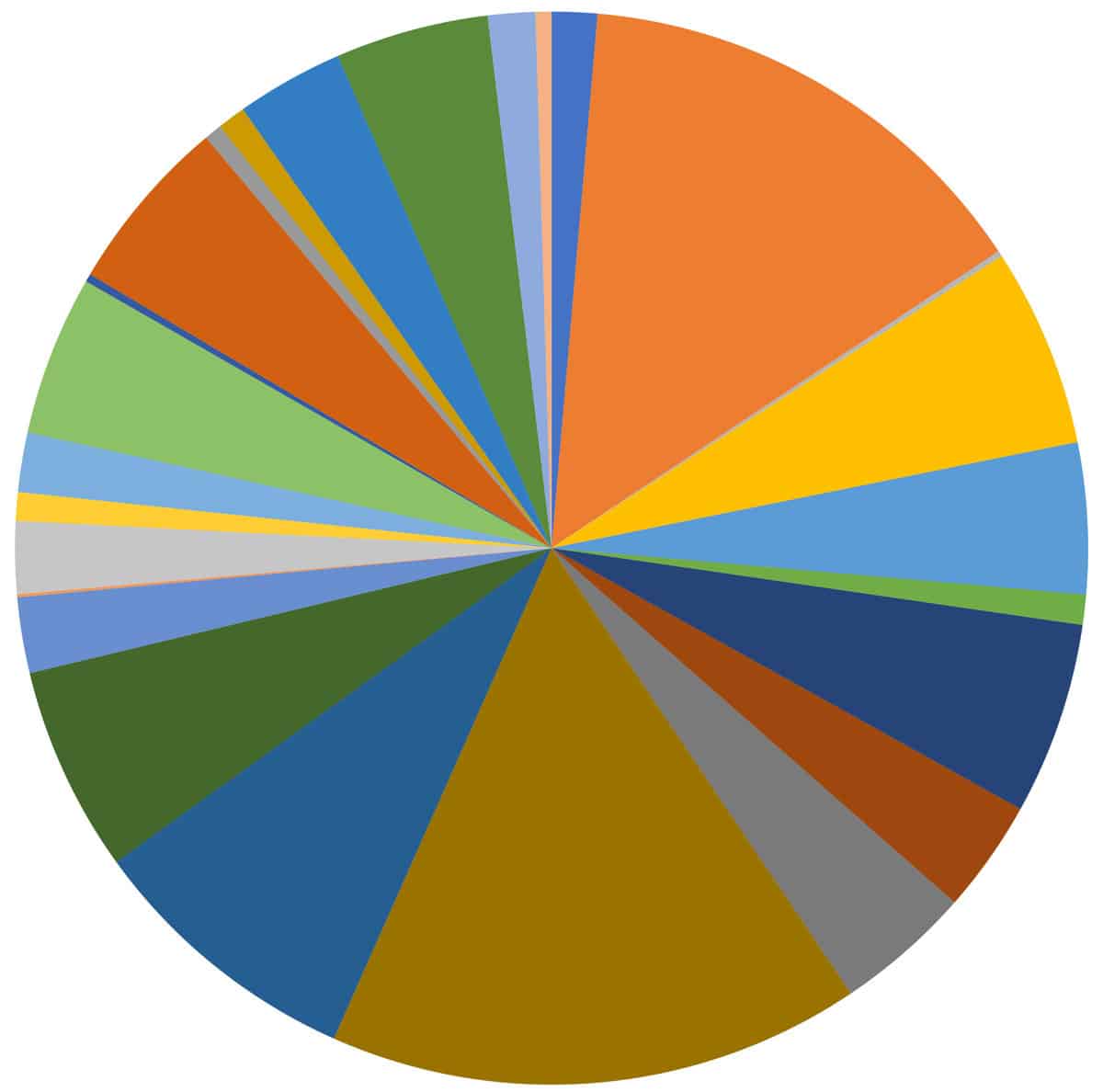
Building utilization
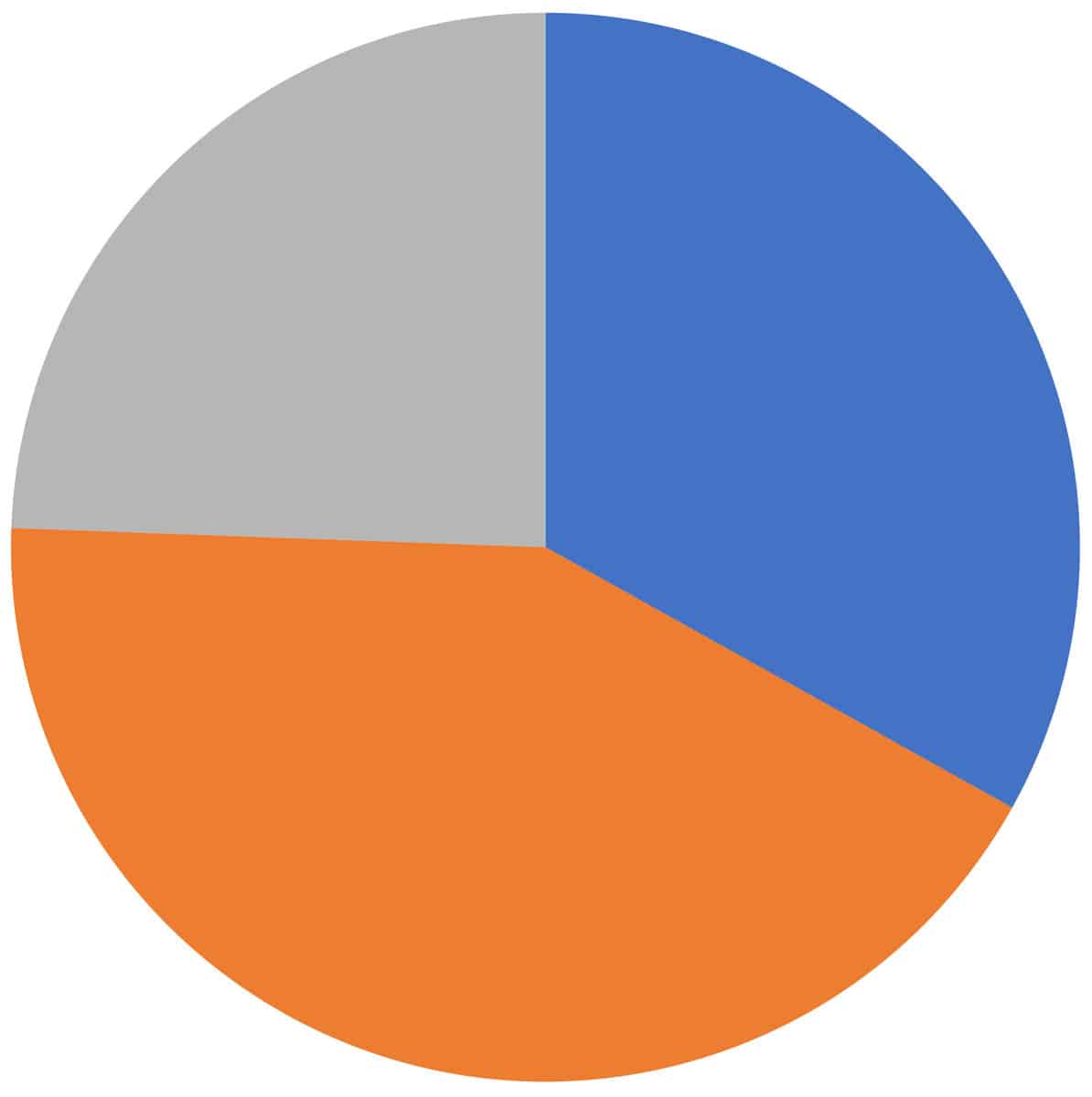
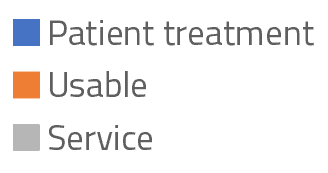
QUANTITATIVE DATA FOR IMMEDIATE TENDERING OF RENOVATION
If it can already be seen that the efficiency of a given building can be substantially increased, or even just a part of the building needs to be renovated, then all the data from the OrthoGraph models is immediately available for a tender. Floor, wall, plinth and paint surfaces, either by type of cladding, by room function, or a combination of the two. In this way, the “idle time” of the buildings can be reduced, ie renovation work can be significantly accelerated even with the start of tendering, while the floor plans provide an accurate and good basis for redesign. During construction, it is worth recording the changes before the covering, because this will create huge value during future operation. It is also worth mentioning the typically 10-15% savings that can be achieved by accounting the real quantities with the surveyed surface data and inventory lists.
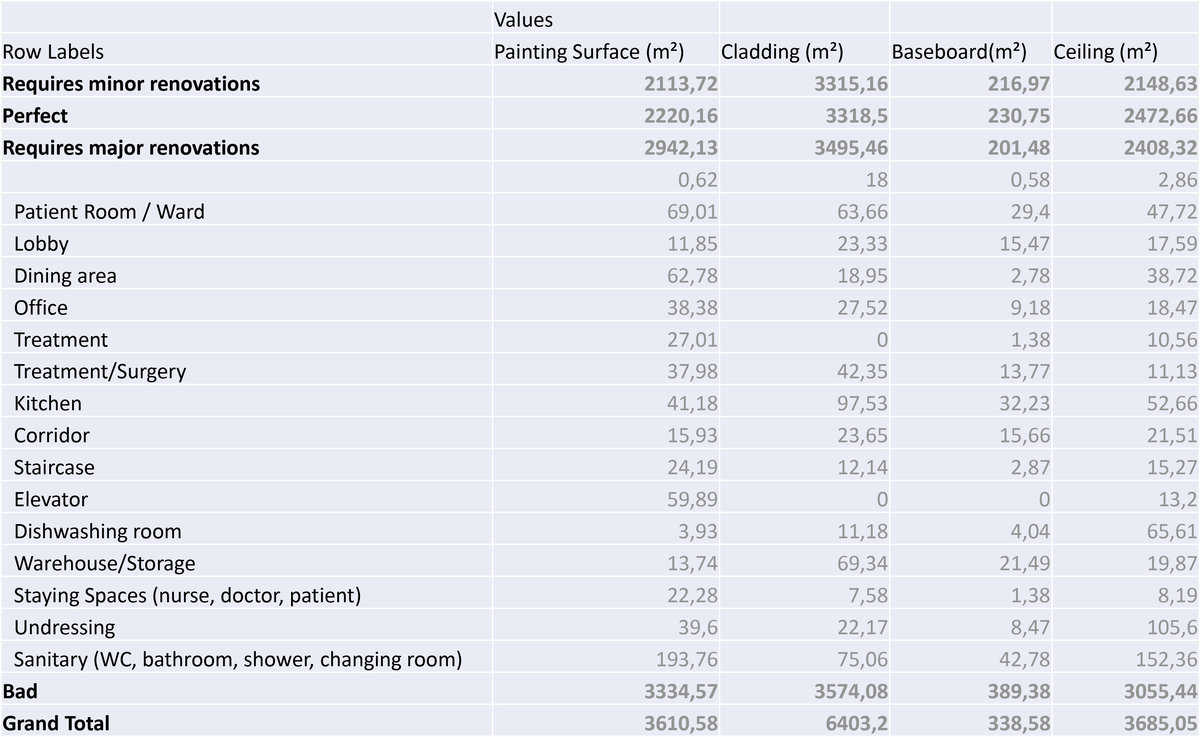
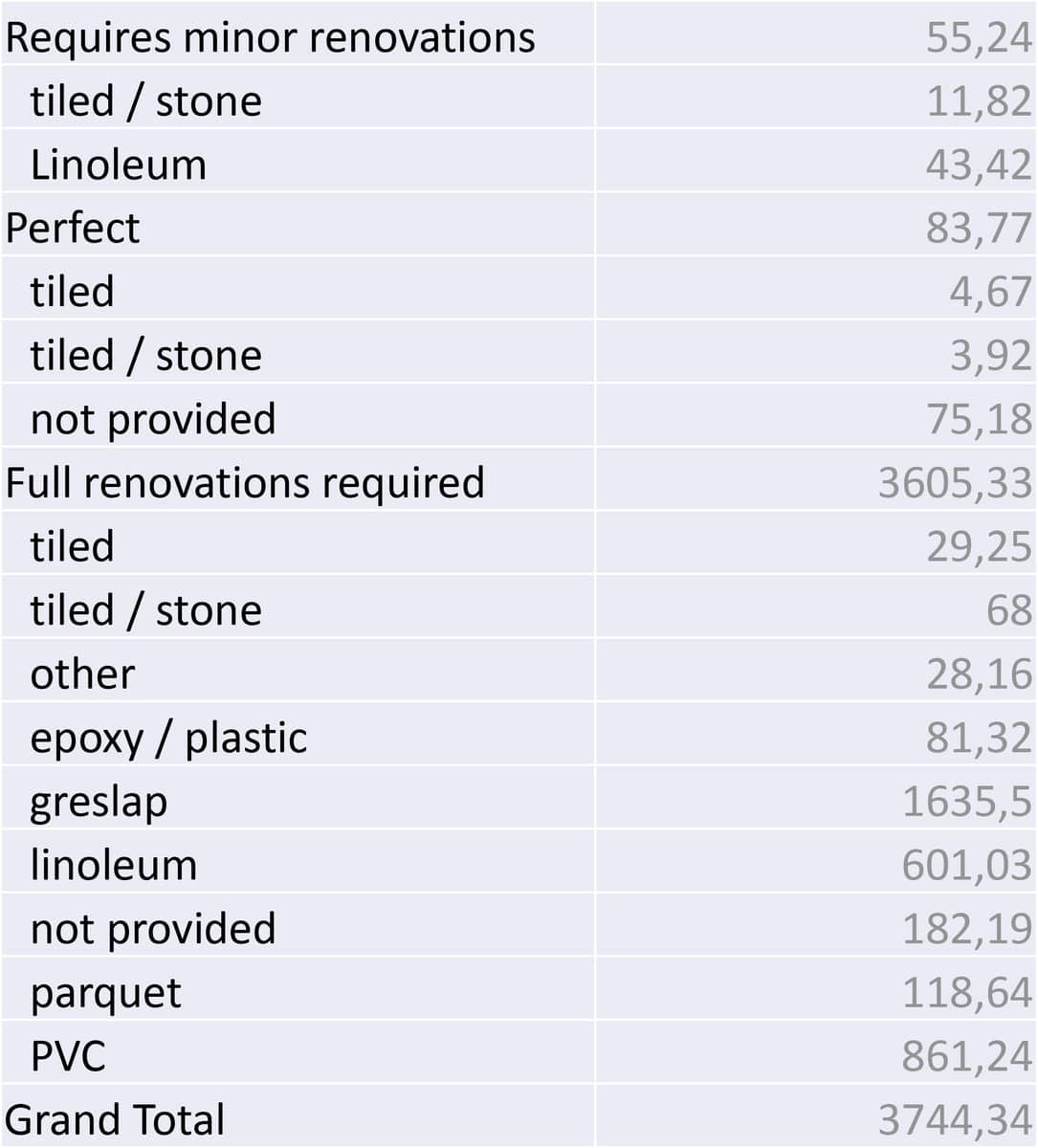
Equipments per condition
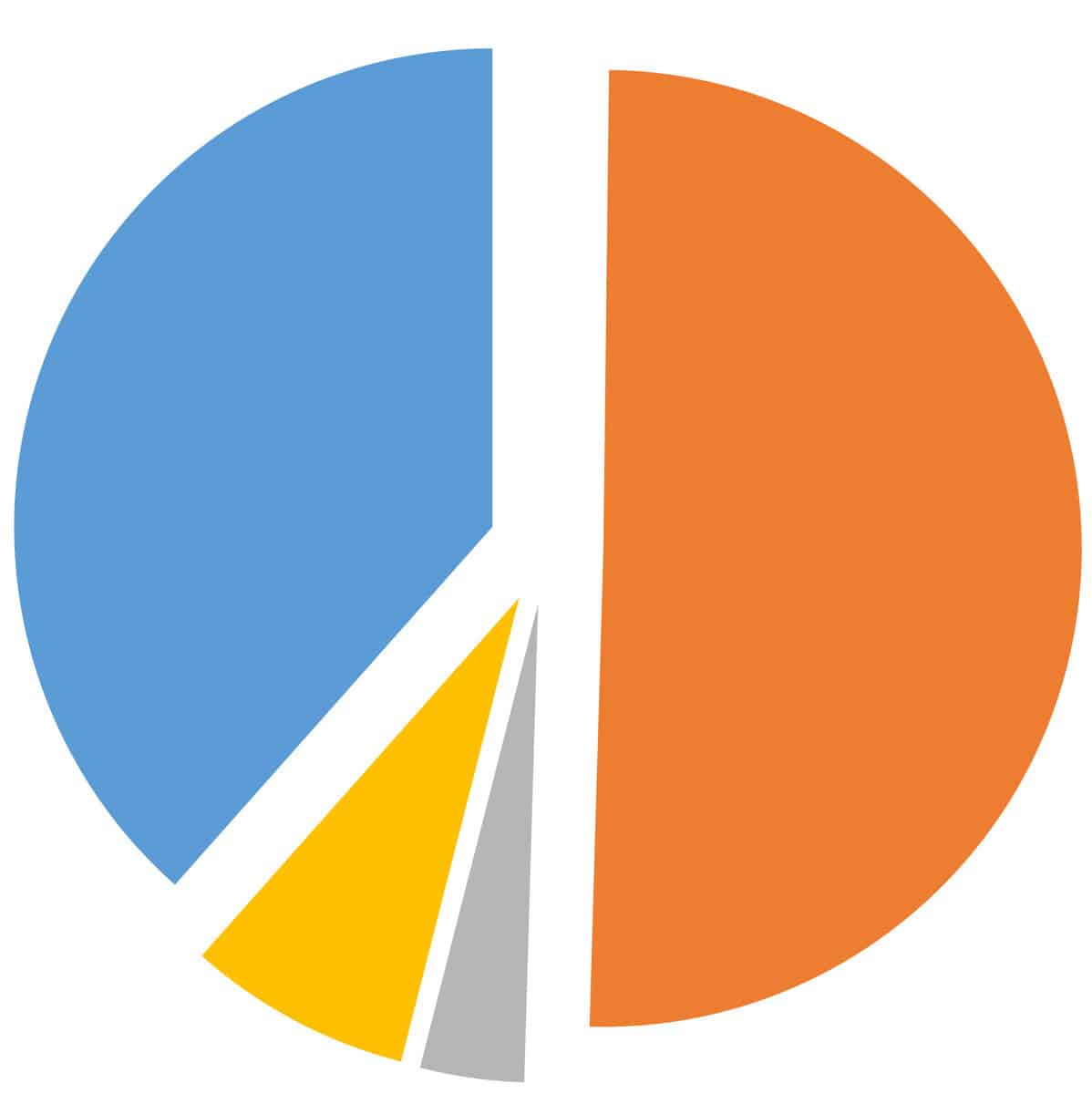
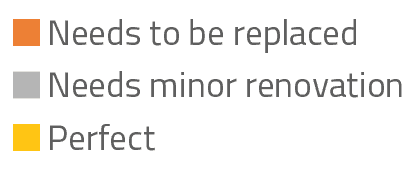
This also includes the fact that since the OrthoGraph system makes it easy to record the condition of the premises and equipment, it is immediately possible to plan item by item exactly what needs to be renovated and what is in a sufficiently good condition, i.e. it can be omitted from the renovation plan and thus also from the costs. We are talking about a lot, because there are no new equipment acquisition costs, demolition, waste management costs and labor costs on these premises or equipment. In most cases, this item alone will repay all the measurement costs of the entire building.
ANALYSIS AND FAST DECISION MAKING
With accurate data, all running contracts and related costs can be reviewed immediately. Cleaning contracts can be reviewed with the knowledge of room categories, flooring and cladding types and door and window surfaces quantities, the lease contracts with real rental areas, but real estate savings can also be seen if we only see the actual, usable net area from the model immediately.
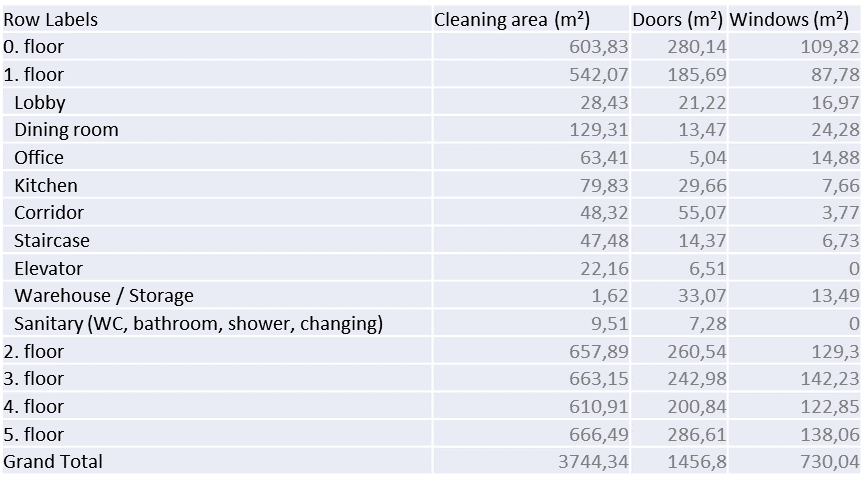
Process support
Here comes the question; how to keep the building documentation up to date, as today in most cases this can only be achieved with a huge amount of work, cost and dedicated resources. With the help of OrthoGraph, the cost of this can also be significantly reduced while increasing the level of service.
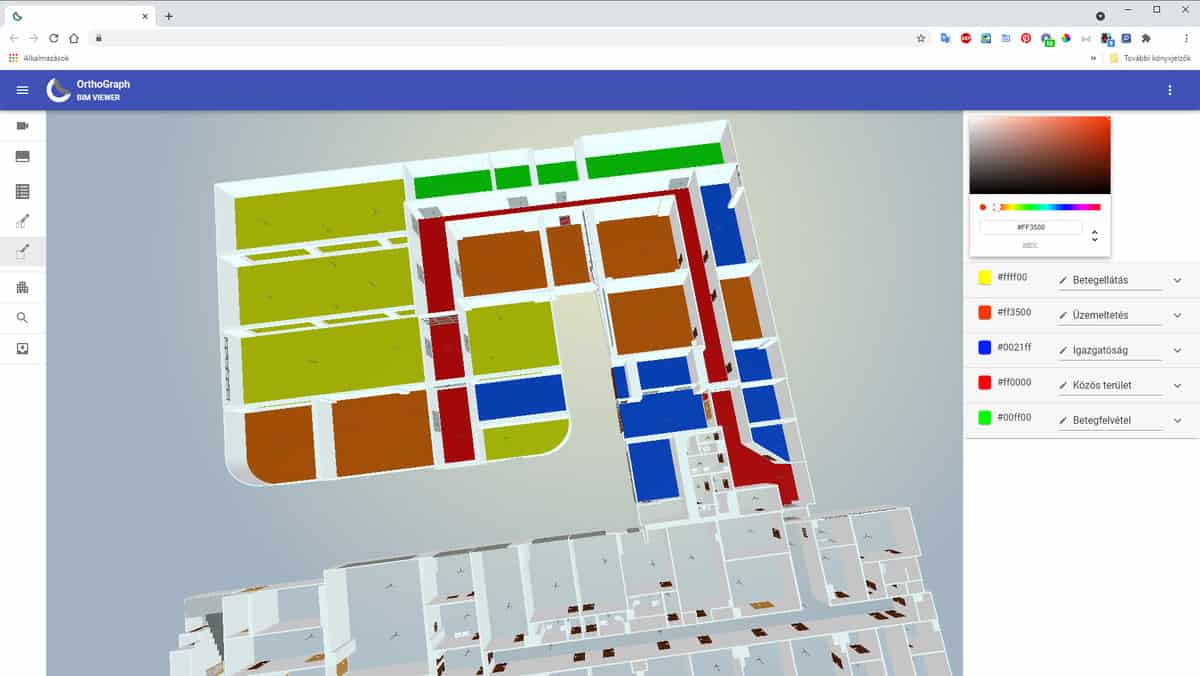
Operational BIM is available to maintainers on-site and to decision makers in the office in a simple browser. By including a reference to the maintenance point during sending the work release, the mobile device immediately shows the referenced equipment on the floor plan so that it can be found quickly. You can also use RIFD or barcodes to make sure your maintenance colleague is repairing the right equipment — and whether they’ve actually gone to the site — and then register the changes to the BIM model right away. This central digital knowledge base allows the building information to be gathered in the Operational BIM system instead of the heads of your maintenance crew. If the maintainer checks the BIM documentation of the maintenance point beforehand, and goes to the site with the right parts and tools from the warehouse – saving a few trips – using the attached photos and even videos, it can help to get the job done faster, better and also making it safer.
Learn more about Orthograph Operational BIM technology in a 2-minute video
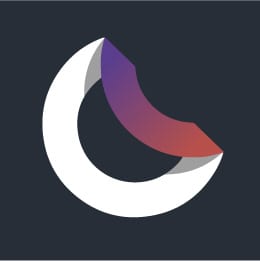
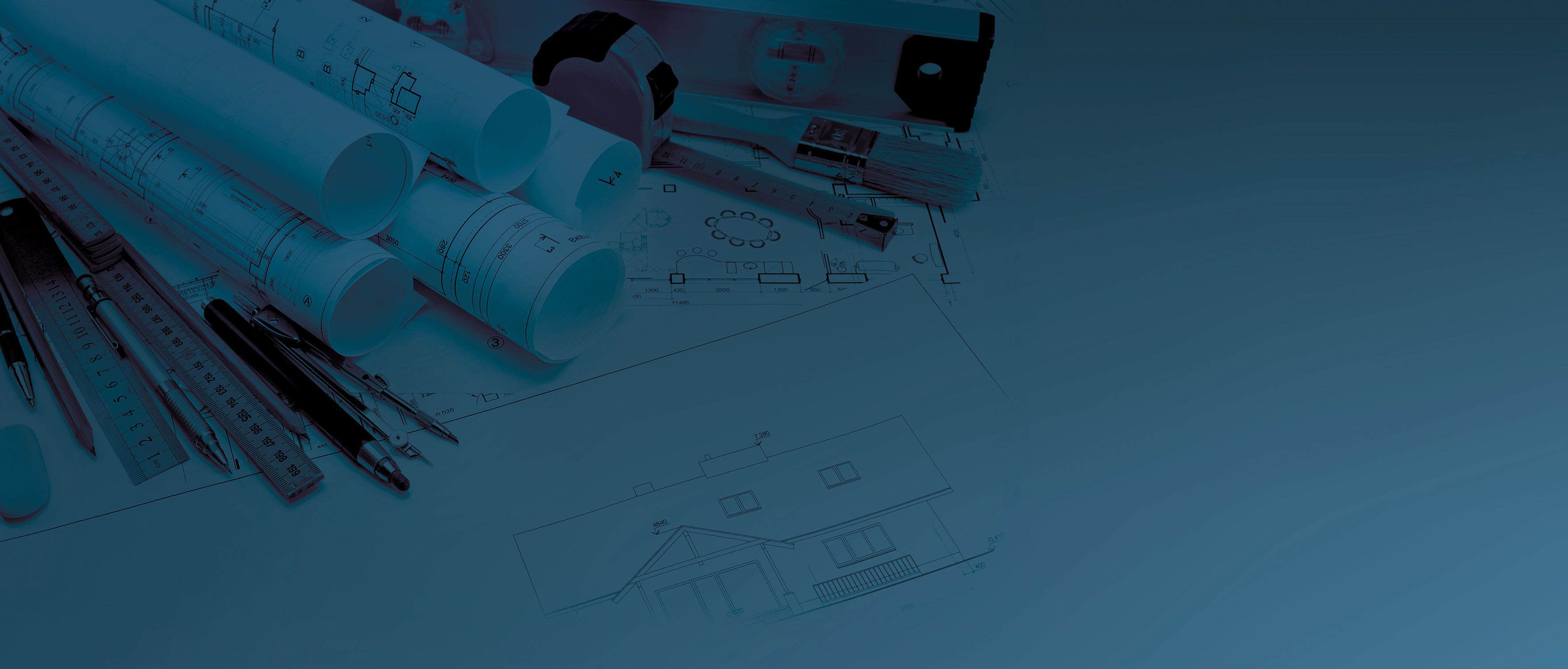
to our Newsletter
OrthoGraph

Contact us
Contact us
OrthoGraph GmbH
Gartenstrasse 7
Zug
Switzerland
6300
+ 41 (41) 5510150
9:00-18:00 Zurich Time
USA: +1 760 933 1550
UK : + 44 (20) 34119438
Other pages
Education
Rapid Survey Concept
Orthograph for Constructions
Historical Building Survey