Is unplanned downtime a major risk for your production? Do you frequently change your production lanes? Imagine having a powerful solution at your fingertips: a centralized knowledge hub for your entire production facility. A Digital Twin that not only reduces or prevents downtimes but also ensures you’re no longer reliant on the knowledge locked in the minds of your maintenance team and suppliers. With always up-to-date data, maintained easily on-site by your own technical staff, you’ll stay in control of your production efficiency like never before.
Both pharmaceutical factories and factories of the food industry all work with hazardous materials, and have extremely high expectations in clean areas. The technology used there is sensitive and any mistakes might cost high amounts, even human lives might be at risk.
OrthoGraph and Operational BIM not just targets the cost reduction in these segments, but also provides a tool that can strongly reduce risks both in terms of downtimes and also human safety during interventions.
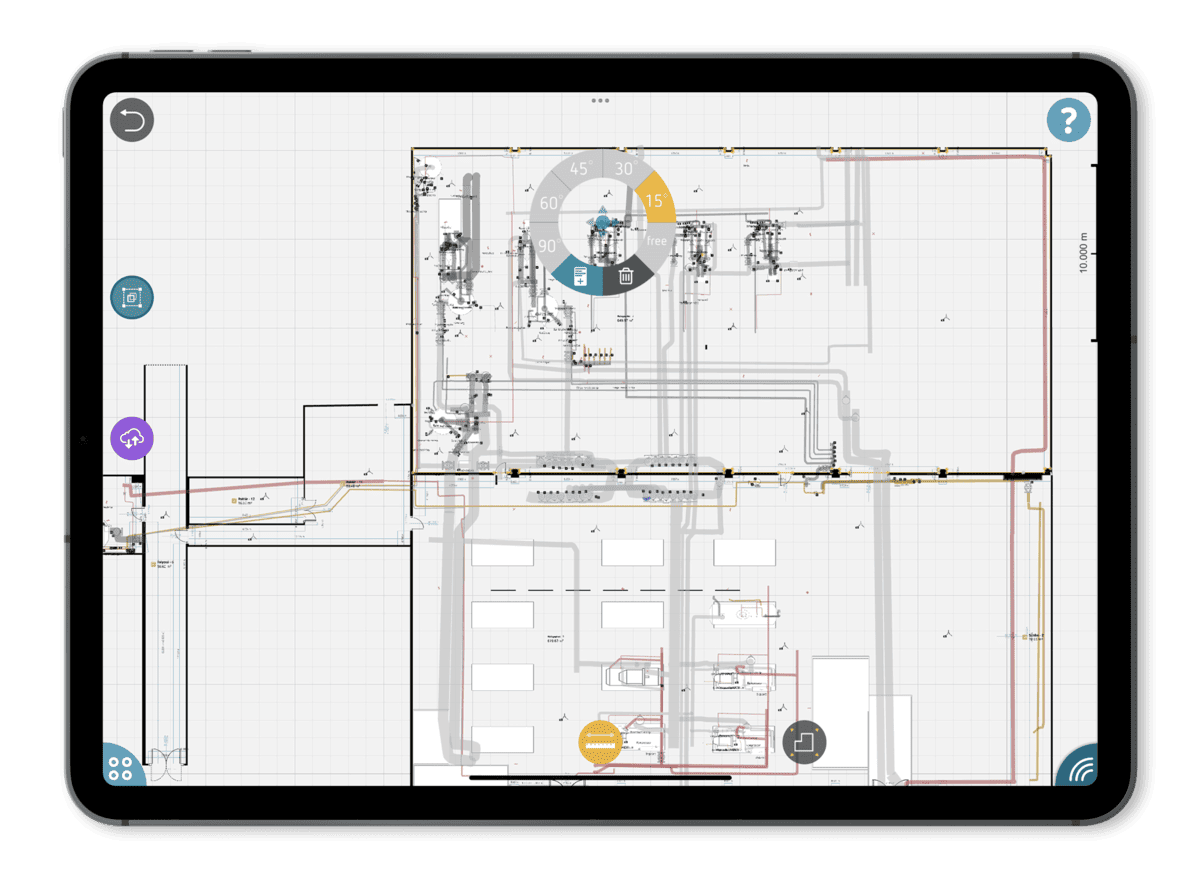
Saving human lives:
Imagine that you have a detailed 3D model containing all pipes, valves, meters and all units that is a part of maintenance operation, they contain QR Code or RFID unique identifiers on them and all important parameters are stored with them digitally. Also you have panoramic photos at every important position. Imagine that all this data is collected within weeks and can be kept updated by your maintenance crew as part of their normal operational work with ease.
Now this saves time and minimizes risks thus save lives at the same time.
Saving money:
In many cases the most time in operation is spent on finding the proper equipment. In addition, it might also happen that not the proper object is maintained, but a similar one in its neighbourhood. Have you experienced that before? This can even be understood as finding the right valve in the forest of valves is sometimes a pretty hard challenge.
In OrthoGraph all maintenance points have their own reference links and we also recommend using unique identifiers on all assets. To send out the maintenance person to the proper valve just send the related link to it, and OrthoGraph will show it instantly. Both the technician – by using an iPad -, both the leader – in a web browser – sitting in the office can see where is the particular maintenance point is in 2D and 3D.
This significant time saving means the same people can do more, and also as we have everything electronically documented, you can expect the same quality of service independently which professional does the maintenance.
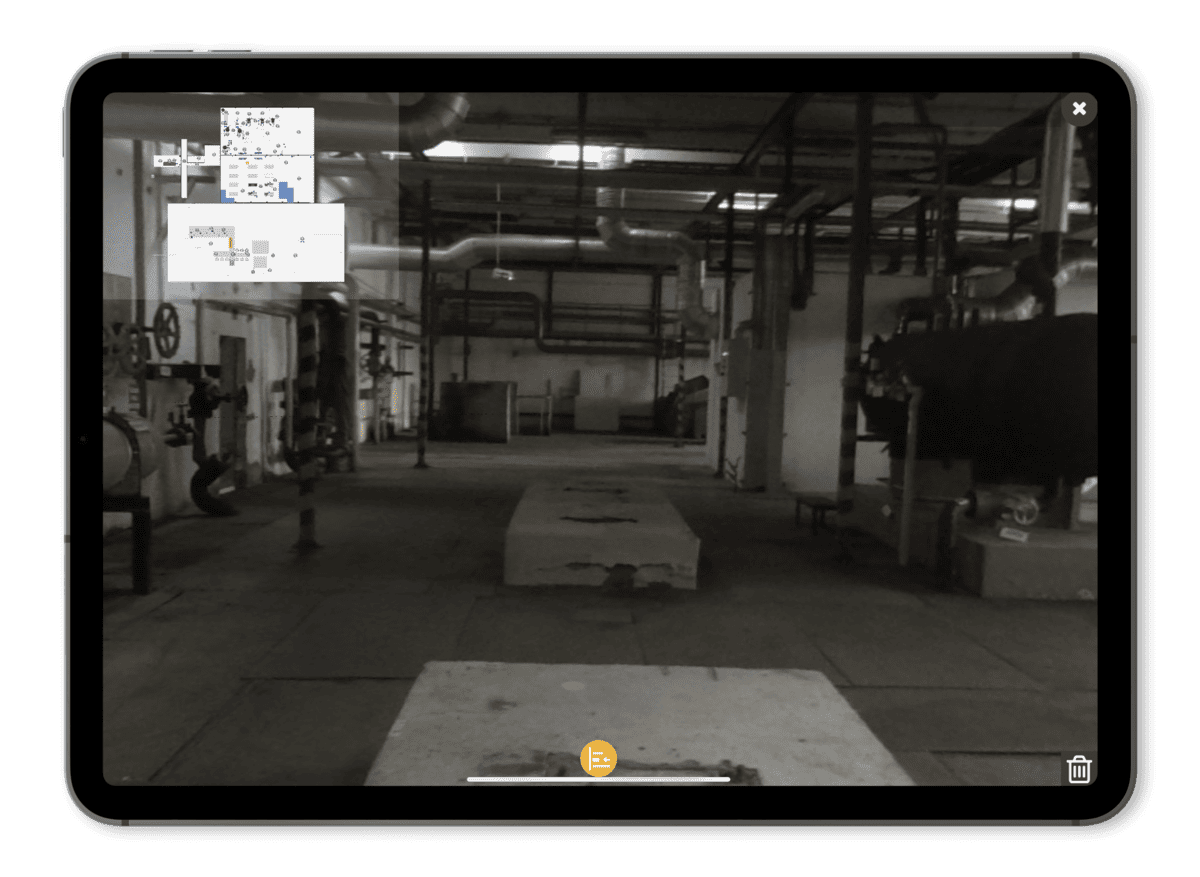
Knowing that the right equipment was repaired:
We always emphasize the importance of using unique identifiers on every maintenance point. Not only on each machine, but maybe even on different parts of it, if that’s so critical to control what’s happening with that. By requiring to scan the given RFID / QRCode / barcode by the technician ensures that the proper object is going to be maintained. Even more, if there is an SLA contract with a subcontractor, then we can even register when the given object has been accessed.
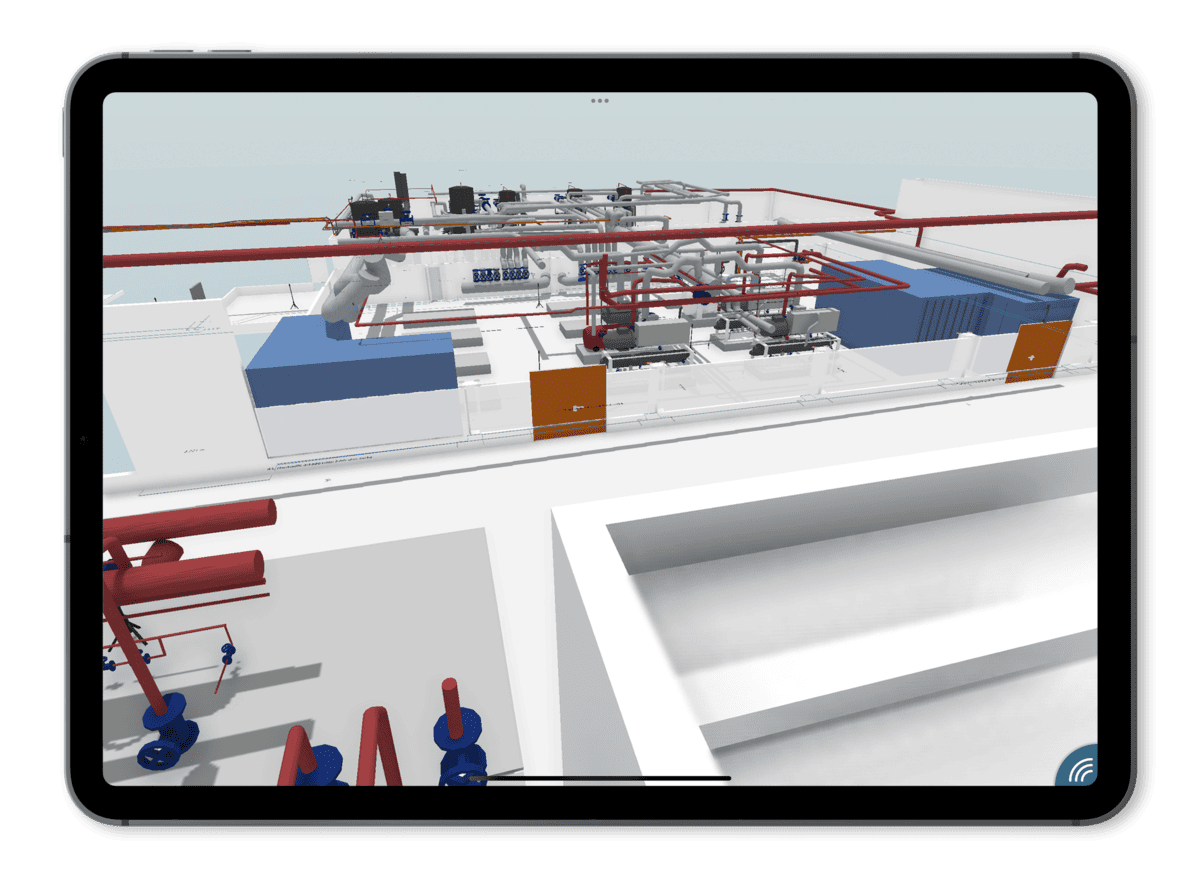
Keeping the data updated:
Gathering the building and asset documentation is a time consuming work, but keeping it updated is even harder. Actually, not anymore. OrthoGraph is that simple to use, that it can be learned in hours how to update all inventory changes, object moves, replacements in the factory. This means any technician who does a repair can easily document the changes, make and attache new photos to the given equipment thus providing an always updated building and asset documentation. This means independence, as if anyone is getting a new task to be done on a given object, it will be easy to find, and all attached properties, documentation can be accessed by using OrthoGraph. Prior or right at the place of work.
When a production chain is modified, rebuilt, moved, then all these changes can instantly be recorded in OrthoGraph so that all connected systems – CMMS, automation, monitorin etc. – can be notified about the changes. Later, if there is an overtemperature, an overpressure, then everybody will know where is it happening and can act in the fastest possible way.
Floor plan changes might also happen sometimes. Walls, doors, windows are modified. This can also be recorded by own employees, though we recommend choosing for this those technicians, who have the most talent for technology. As inventory changes is as easy to write a post on any social media platform, changing the main floor plan elements needs a bit more. Not much, but it needs a 3 days long training to learn how to do it in a professional, digitally controlled way. There is no need for architectural knowledge, education, but a good 3D understanding, reading a floor plan is necessary for that. Following up these changes with the proper knowledge takes again only hours, maybe a day, but not more.
Integration – making the most out of Operational BIM:
Data only generates value if it is used and maintained. OrthoGraph is a platform of data warehouse. Any system that needs building or asset data, graphical representation, maybe graphical reporting can integrate with OrthoGraph. For this the API is free to use, free to integrate. The more system connects to OrthoGraph the more value it can generate.
A proper integration to a CMMS system gives rapid and controlled workflows – also by using the unique identifiers on all assets -, a building or machinery automation system can monitor easily what’s going on in the factory, and can react fast if there is something out of range. Even a financial system can run graphical reports on the worst or best performing machines that should be compared to the other ones to bring performance to the highest level.
Speaking about reports bring out the most of the integrated Operational BIM ecosystem by continuously analyzing data. AI could do a lot, but a person with good financial approach can do it even today. We intentionally don’t call it a BIM manager, as this should not be someone having architectural or civil engineer knowledge, rather a process oriented thinking person with financial way of thinking can better find those points, that have a critical affect on current performance. With this approach by using reports, highlighting the weak points OrthoGraph Operational BIM controlled by this person can instantly generate money by the improved performance.
What else do we get, if we use unique identifiers, RFIDs / QRCodes or barcodes on all maintenance points?
Exact element identification and workflow control. If we have an important object, equipment that needs to be touched for any reason, then these unique identifiers can help to easily identify the given object. If we use the proper workflow based issue tracking system that is based on using these unique identifiers, then the site worker can be requested to scan the given equipment’s identifier to confirm that the proper one is going to be maintained. If the system is prepared for that, then we even can check the time of work to find our more information about the given work.
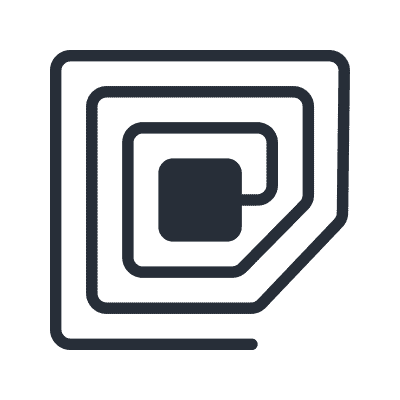
Have you got a similar project in your mind? Have you got further questions? Want know more in a personal meeting or want to start a pilot? Click the button:
to our Newsletter
OrthoGraph

Contact us
Contact us
OrthoGraph GmbH
Gartenstrasse 7
Zug
Switzerland
6300
+ 41 (41) 5510150
9:00-18:00 Zurich Time
USA: +1 760 933 1550
UK : + 44 (20) 34119438
Other pages
Education
Rapid Survey Concept
Orthograph for Constructions
Historical Building Survey
Recent Comments