The Operational BIM©
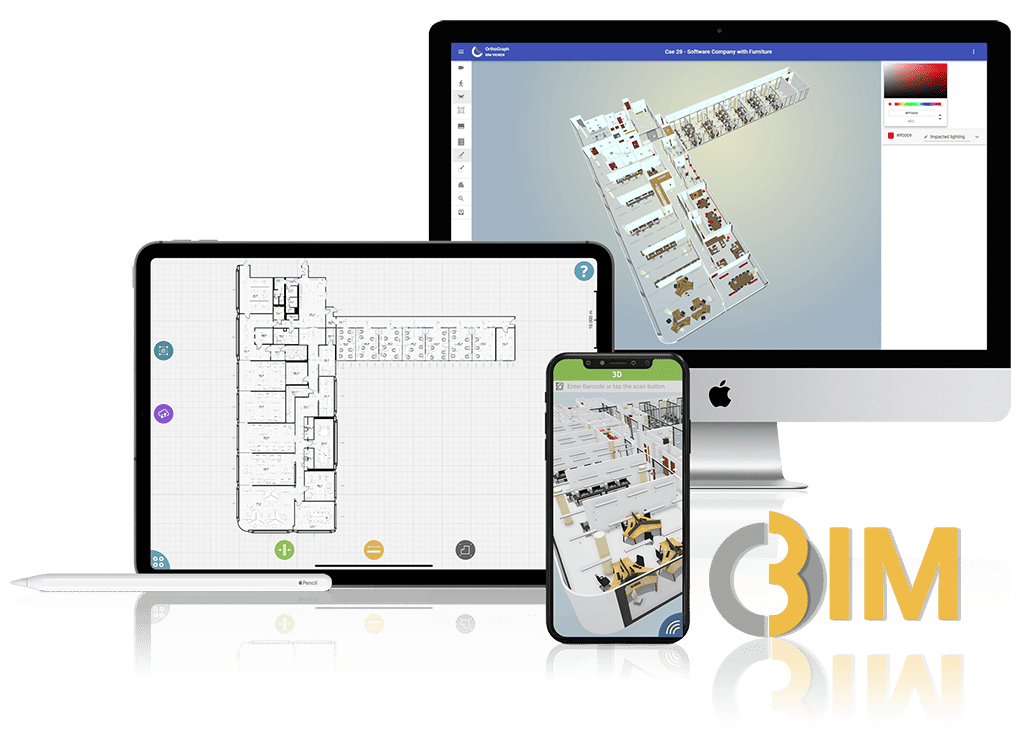
The goal of operational BIM is to rationalize the use of BIM in long-term building operation and extend its use to support the productive activity of the particular facility. It has to be easily surveyed with simple and rugged tools like laser distance meters for the floor plan and barcode/RFID readers for the inventory with all required additional data – including photos. It is key important that keeping these building and asset data up-to-date must be easy, processed by the normal operational crew without significant time need from them at the place of operation/maintenance – so it can become the part of their regular work.
Comparison of BIM technologies
BIM FOR BUILDING OPERATION - OrthoGraph | BIM FOR DESIGN AND CONSTRUCTION SIMULATION | |
---|---|---|
Creation | Quickly assessed and kept up-to-date: The daily survey rate is 1000-2000 m2 daily per surveyor, teamwork is available, based on simple tools like laser distance meters. The result is high-precision documentation, with on-site digital quality assurance both for the drawing and inventory. | Slowly measurable, difficult to maintain: It can be modeled with a daily survey speed of 100-120 m2 using expensive and sensitive tools (such as laser scanners), the same is required for keeping it up-to-date. There is no inventory and it is unfeasible to maintain it with regular tools. There are no valid equipment properties and quality control is unavailable. |
LOI | Ideal level of details for operation:It provides exactly the information that is necessary for daily operation and maintenance work. | Graphic-focused, detailed model: Design oriented, difficult and expensive to maintain, full of data that is not or rarely used in operation, lack of valuable data, such as unique identifiers, properties of assets, photos, panoramas. |
Content | Graphic inventory: Every maintenance point, equipment, production line element, and even furniture can be recorded with their unique identifiers. Elements are equipped with properties, photos, panoramas recorded on site, with continuous digital quality assurance. | 3D drawings, BIM designs: Not the realization, but only the plans can be created, there are no unique identifiers, no attached photos, panoramas, or device properties. There is no on-site quality assurance or data control. |
Maintainability | It can be kept up to date: Even the technical maintenance staff can use it and record changes on-site when and where they happen. | Requires professional user, expensive: Requires a highly qualified CAD operator (typically an architect or civil engineer). |
Availability | Available on-site for work and decision-making: Assists the maintenance staff’s navigation, equipment information is available anywhere, the decision-maker receives graphic reports and building interpretation via a 2D/3D view in the web browser. | Available at the office: CAD operator exports, prints drawings, prepares reports manually and produces IFC files. Changes are recorded on post-its, the decision-makers wait for hours/days for data, which typically arrives in PDF format. |
Flexibility | Integrated:
|
File-based:
|
Performance | Low-performance hardware requirement: Available on mobile devices (iPad, iPhone) on-site or via web browser in the office on regular computers. | High-performance hardware requirement: It requires strong hardware made for CAD management, a strong processor and video card, and cannot be taken to the site. |
Scope | Design and construction support: Saving industry standard IFC, DXF, and Excel help accounting and progress reports and documentation work with up-to-date, controlled quality information. | Design and construction support: Design and renovation support from surveyed data, various high-quality renders are available from CAD systems. Following up progress and deviation from original plans is hardly available. |
Benefits | Content optimized for operational purposes: Unique identifiers, graphical inventory, attached images, videos, and documentation (e.g. diagrams, parts list, etc.), process support, integration to Building Management and other operational systems. | Lack of building and machinery operation-related information: On-site images, equipment information, RFID, and other unique identifiers are all missing to support operation. |
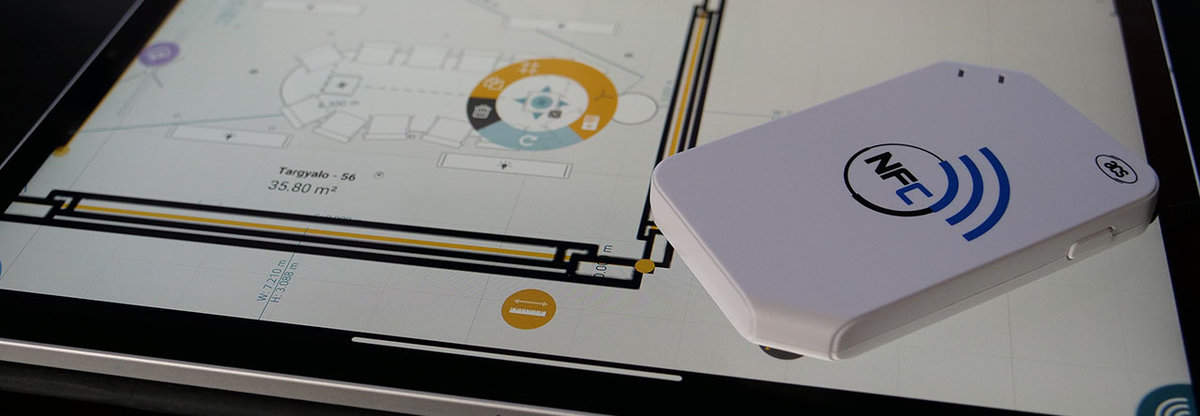
Another key requirement defining the success of BIM in operation is integration. Operational BIM must be embeddable to any software applications and any workflows, processes demanding building or asset data on-site or in the office. So if a maintenance person needs to find an equipment, then the floor plan or 3D model for navigating there must be available on-site, but for a decision maker to see a rental report colorized must be accessible in a simple web browser from anywhere. All this data should be accessible and modifiable on-site by several users at the same time.
As the Operational BIM is meant to follow up all the changes of a building or an asset in it, it should preserve the “building history” in log files.
Fulfilling all these requirements have been our key driving preferences when developing the OrthoGraph Enterprise ecosystem. The use of Operational BIM results in significant cost savings in the everyday operation while increases the productive performance of the involved facilities.
Read more about the benefits of using Operational BIM in more than the facility management e.g. for office buildings, shopping malls, hospitals, production facilities etc. in our study.
The 3 pillars of Operational BIM
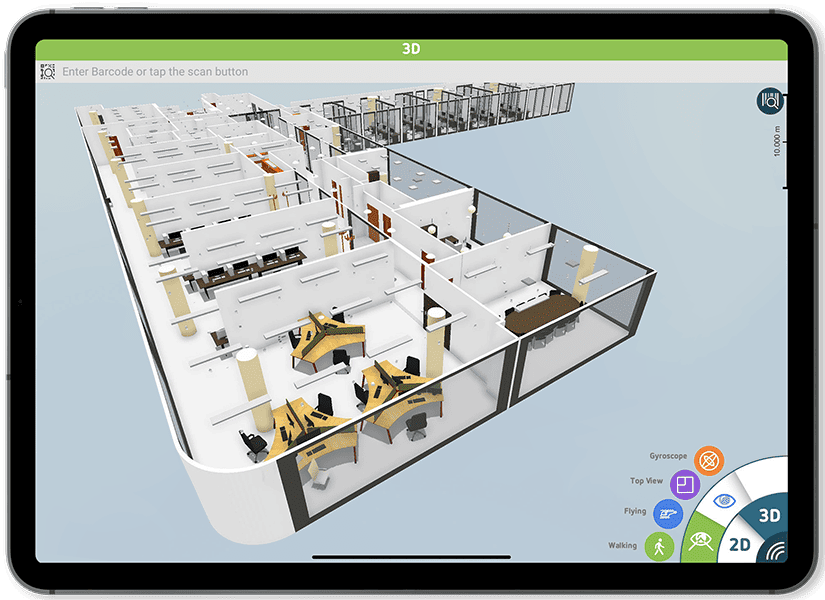
Buildings & Assets digitized in CAFM
High speed and high accuracy
OrthoGraph = Simplicity
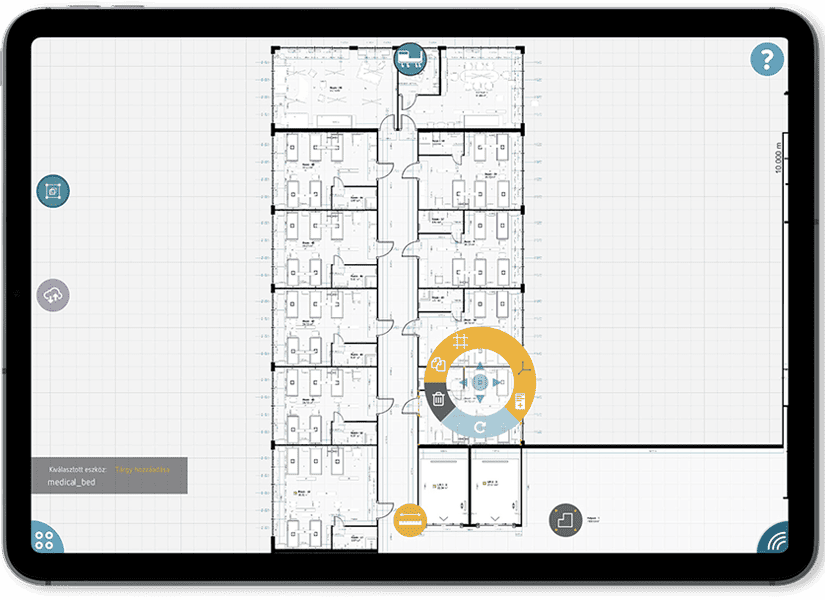
Operational workflows simplified by Digital Twin
Navigation, Barcode/RFID,BIM information available atthe place of work
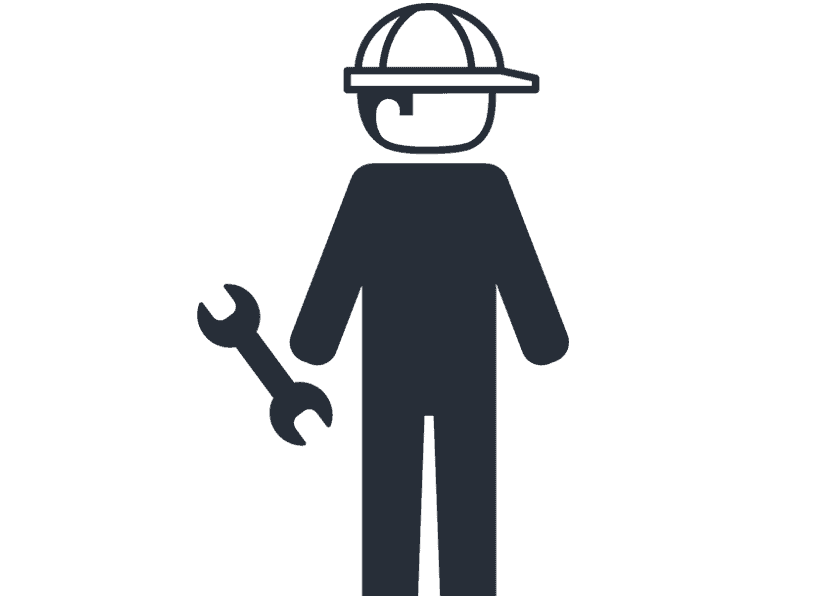
All building and asset data updated on-site
By the regular maintenance crew
No special knowledge required
We help you save the total construction cost of your building!
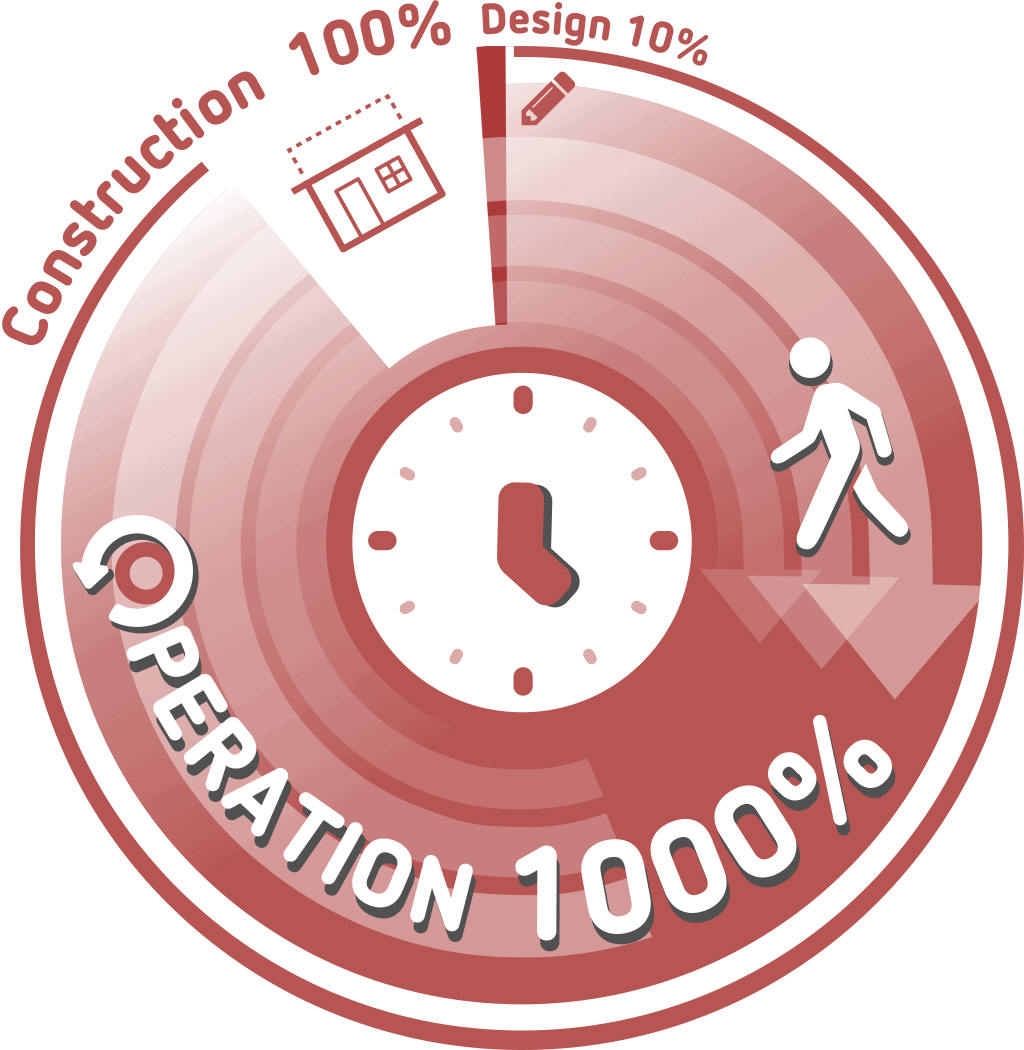
The longest and most expensive part in a building’s life-cycle, is the 30-50 year long period, when the building is in-use, operated. The total cost of this period is approximately ten times as much as the building’s construction cost. By using OrthoGraph’s technology to facilitate building operation you can save up to 10-20% of all these continuous costs – which amount is in the range of the original construction cost.
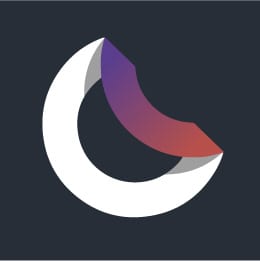
By providing your e-mail address we give you a free access to this detailed document mentioning the benefits of using BIM in different areas effortlessly.
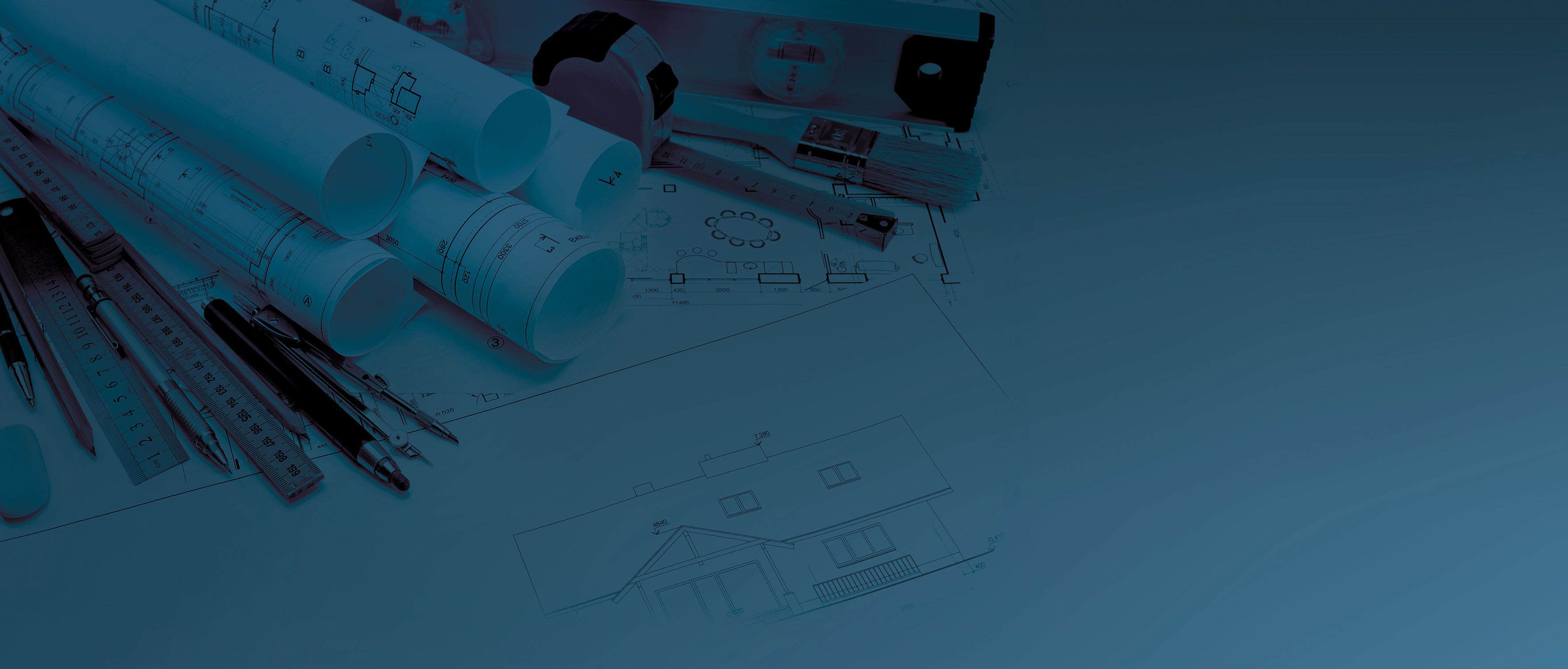
to our Newsletter
OrthoGraph

Contact us
Contact us
OrthoGraph GmbH
Gartenstrasse 7
Zug
Switzerland
6300
+ 41 (41) 5510150
9:00-18:00 Zurich Time
USA: +1 760 933 1550
UK : + 44 (20) 34119438
Other pages
Education
Rapid Survey Concept
Orthograph for Constructions
Historical Building Survey